Where are cutting tools and the technologies around them heading?
Two of the leading cutting-tool makers prepare for the future of part-making. We take a look at recent innovations—with a close eye on where tools are heading.
From proprietary aerospace metals to polymers and carbon fiber composites to 3D-printed parts from metal powders, the materials of tomorrow are evolving.
Where are the cutting tools and toolholders to handle these materials heading? Will cost, tool life or predictability be the driving factor of new tool development?
How important will real-time feedback from tools become? Is Industry 4.0 and the Industrial Internet of Things only hype, or are we at the cusp of a game-changing evolution in metalworking technology?
Whatever the outcome, cutting-tool suppliers and manufacturers are embracing this brave new world.
Cutting-Tool Trend #1: Internet of Things Integration
Anyone who’s not asking these questions might look back 10 years from now and wish they’d done things far differently. Not only are most cutting-tool makers cranking out new carbides, coatings and geometries at breakneck speed, but many expect digitalization to become the clear path forward for shops wishing to increase productivity in the face of a more technologically minded workforce.
Among them is Sandvik Coromant. The company has been quite busy developing an entire ecosystem of dashboards and visualization tools to help customers leverage the supposed benefits of Industry 4.0 and the IIoT. Its CoroPlus connected-solutions platform, for example, promises to deliver never-before-possible insights into machine tool utilization and other efficiency metrics. In a similar vein, its DTH Plus-driven toolholders provide predictive maintenance capabilities designed to reduce downtime on mill-turn CNC lathes.
Magnus Ekbäck, Sandvik Coromant’s vice president of strategy and business development, delivered a keynote speech at IMTS 2018 describing how digitalization is poised to reshape discrete manufacturing.
He discussed the major trends affecting the industry, including the demand for more information, the growing skills gap and the need for better decision-making in the design and planning stages. Each of these, he said, can be addressed through greater connectivity and access to data.
Cutting-Tool Trend #2: Vibration Reduction in Turning
One notable example of this is the toolmaker’s Silent Tools Plus program, designed to reduce vibration and improve hole quality in extended-reach internal turning operations. Practically all major tooling manufacturers offer some type of damped boring bar technology for this often troublesome application.
Sandvik Coromant has taken it one step further by equipping its tools with Bluetooth-capable sensors along with a mobile “app” to actively monitor boring conditions.
As Ekbäck noted, manufacturing design and planning will play an increasingly important role in machine shops of the future. Cloud-based utilities such as Sandvik Coromant’s CoroPlus ToolGuide and ToolLibrary will serve to streamline toolpath programming, and then help operators optimize machining processes long before the first chip is made.
Kennametal’s NOVO program offers similar capabilities with its “Art to Part to Profit” suite of digital tools. Users can select and download digital models of cutting tools and toolholders, receive advice on how to apply them, simulate and fine-tune their performance.
Cutting-Tool Trend #3: End Mills, Drills and the Chip-Thinning Effect
There’s no shortage of tools to choose from: Kennametal is just one of the companies to have introduced a slew of high-performance, application-specific end mills and drills in the past year. The KOR 5 coolant-fed, five-flute, chipbreaker-equipped carbide end mill is advertised as the “king of roughing” in aluminum.
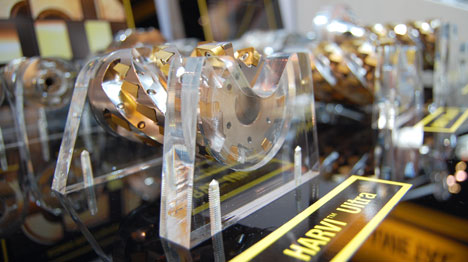
Source: Better MRO
The HARVI I TE end mill’s proprietary flute design promises similar performance in steel, stainless steel, cast iron and high-temp alloy. The KenTIP FS drill is said to provide solid carbide performance in a cost-effective modular design. And indexable cutters such as the Mill 4-12KT and HARVI Ultra 8X continue to raise the bar on high-performance milling.
Sandvik Coromant hasn’t exactly sat on its digital laurels alone. Its CoroDrill DS20 is designed for deep and high-precision drilling, while the CoroDrill 863 targets aerospace holemaking in carbon fiber reinforced plastics and the metal-stacked aluminum and titanium found in aircraft frames.
What’s perhaps more notable is Sandvik Coromant’s role as a cutting-tool disruptor. Its CoroCut QD parting tools leverage the Y-axis on high-end CNC lathes to significantly increase tool life and feed rates in cutoff applications. Similarly, the CoroTurn PrimeTurningTM takes advantage of the chip-thinning effect, which is the same phenomenon that makes trochoidal milling strategies so successful by turning parts in a completely unorthodox direction: away from the spindle.
Cutting-Tool Trend #4: 3D Printing in Manufacturing
Each of these cutting-tool giants is pursuing another innovative toolmaking strategy using a technology that an increasing number of manufacturers are familiar with: 3D printing.
Sandvik Coromant saw great success at autonomous vehicle maker Local Motors with the CoroMill 390, a lightweight, additively manufactured indexable milling cutter that reportedly reduced milling time on a composite shuttle chassis by 95 percent. And thanks to the quick-change Capto head, setup times were reduced.
Kennametal is also using 3D printing. When a customer struggled to ream a pair of coaxial bores in an electric motor housing because the tool was simply too heavy for the machining center, Kennametal engineers designed and 3D-printed a custom indexable reamer that not only reduced the tool’s weight by half, but achieved the automaker’s demanding accuracy, roundness and surface finish requirements.
These success stories represent another trend: custom tooling. When off-the-shelf tooling doesn’t quite cut the mustard or where greater productivity is called for, these cutting-tool manufacturers use their deep engineering knowledge to help find solutions. These might include something as basic as an indexable drill-chamfer-spotface combo tool, or it could be a 3D-printed lightweight reamer.
Whatever the need, additive manufacturing will have a profound effect on cutting-tool suppliers and those who use their wares alike. So to answer the “which is most important: cost, tool life or predictability” question posed earlier, the answer is obvious: It’s all of them—with data visibility and connectivity for good measure.
What innovations in cutting-tool technology interest you the most? Speak your mind and ask questions in the metalworking forum.
Talk to Us!
Great article!! Very well put together and an interesting read!
43Glad you found it informative Bobby. Thanks for visiting.
42You made a good point that cutting tools are important to have when getting into 3D printing. My husband is planning to buy new custom machine shop tools soon because he has a lot more space to work with after getting his workshop renovated. Perhaps it's also time for him to delve into 3D printing.
https://kochmachinetool.com/
44Leave a reply
Your email address will not be published. Required fields are marked *