A recent upswing in aircraft orders together with rising passenger numbers indicates a recovery is in store for the aerospace industry. Will your shop be ready to capture the growth opportunities?
Tooling Up for an Aerospace Industry Recovery: Is Your Shop Ready?
United Airlines recently placed its largest airplane order in the history of the company. It was also the biggest order by any airline in more than a decade.
In addition, U.S. passenger numbers are edging back to pre-pandemic levels, indicating that America’s traveling public appears ready to take to the skies again.
All of this is great news for the aerospace industry, which is why manufacturers, and their suppliers, should start planning now for upcoming growth opportunities.
Practically every major cutting tool and tooling supplier today provides solutions that will make machine shops, fabricators and specialty suppliers more efficient and profitable, whether they’re focused on aerospace or not.
Joining with the Experts
Much of this change centers around the use of strong yet lightweight materials such as advanced ceramics and composites, which is why anyone gearing up for the aircraft of the future should be knowledgeable in working with them.
One good place to learn about the bonding, fabrication and protection of these and other materials is 3M. The St. Paul, Minnesota-based manufacturer and aerospace supplier has significant expertise in this area, and offers educational courses to the public through its Transportation Academy.
Read more: How Do I Avoid Costly Spindle Repairs? Increase Machine Uptime with These Three Steps
Seco Tools notes that titanium and heat-resistant superalloys (HRSA) will continue to play a key role in aircraft manufacturing going forward.
Like 3M and many other manufacturing suppliers, Seco offers extensive learning assets on its website, many of them focused on aerospace challenges and solutions.
The cutting tool supplier also suggests that it “works closely with aerospace manufacturers to create and provide solutions that increase productivity and bolster profitability,” a statement that certainly extends to their suppliers.
Read more: Small Parts and Precision Machining: Advice from the Experts on Tools and Techniques
Don’t Break the Chain
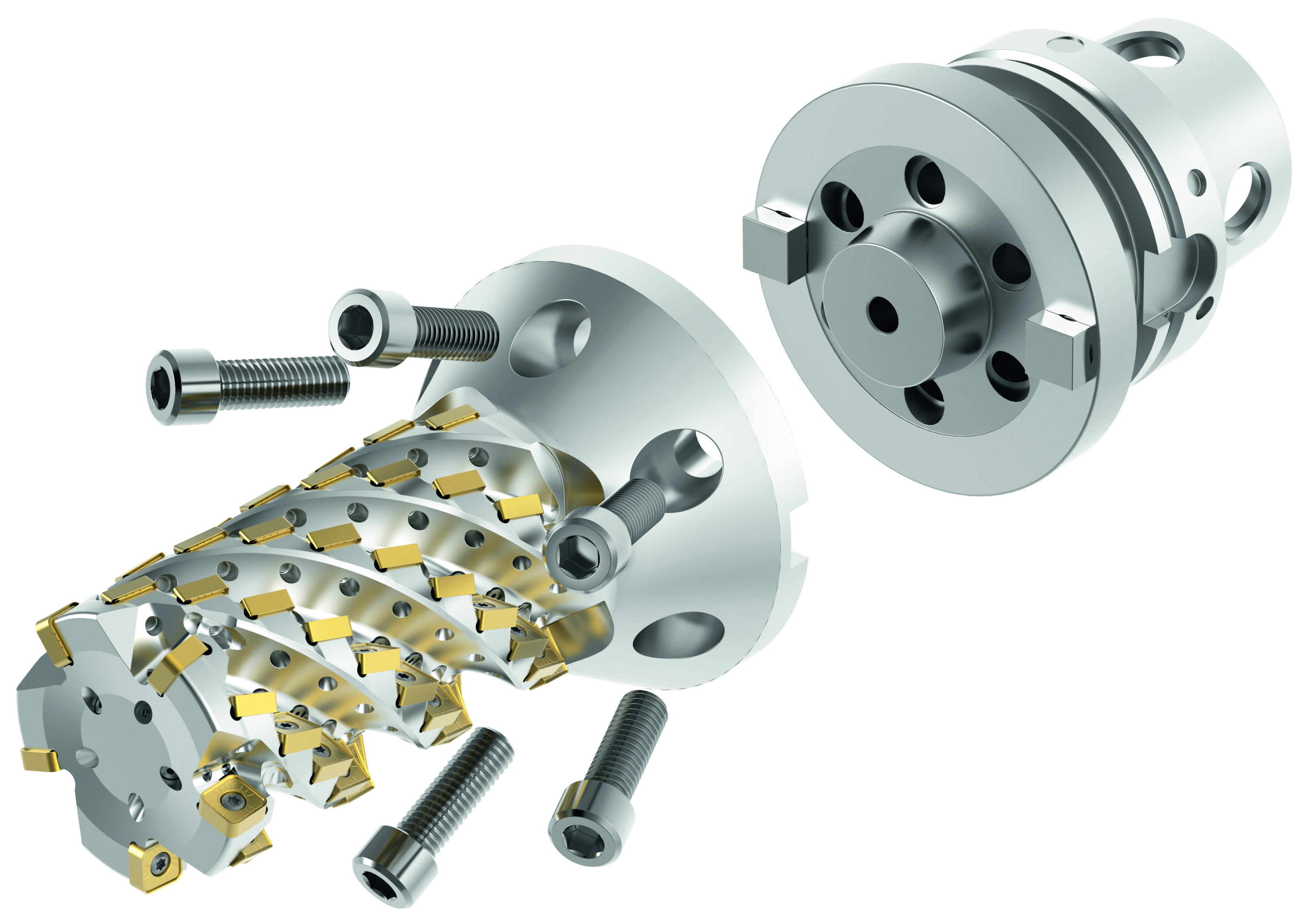
Of course, it’s a good time to be in manufacturing (see sidebar) because practically every major cutting tool and tooling supplier today provides solutions that will make machine shops, fabricators and specialty suppliers more efficient and profitable, whether they’re focused on aerospace or not.
Kennametal product manager Georg Roth has a good solution story, one that addresses the needs of aerospace manufacturers producing structural components such as titanium pylons and landing gear beams.
The three-part tooling approach uses the company’s new FBX flat-bottom indexable drill to “chain drill” a series of starter holes, clearing the way for a rough milling operation with a HARVI Ultra 8X (HU8X) indexable end mill, then finish milling the floor and walls using solid carbide end mills.
The solution is available with a BTF46 (bolt taper flange) connection that fits a range of spindle interfaces, KM4X among them.
“The FBX drill dramatically speeds up the machining process by combining the advantages of a flat-bottom drill and a Z-axis plunge mill,” he says. “The flat-bottom design eliminates radial forces, while four effective cutting edges provide increased feed and speed rates, leading to up to 200 percent higher metal removal rates than traditional ramping techniques.”
Read more: Video: How Has Manufacturing Changed Your Life?
Stay Safe in Your Machine Shop
.jpg)
There’s one additional challenge when machining titanium and, to a lesser extent, aluminum, and that’s tool pullout during roughing operations. Brendt Holden, president of Haimer USA, explains that no matter how much force you apply to a sidelock-style end mill holder, some small amount of tool creep can still occur. Nor is the problem limited to sidelocks—even shrink-fit, hydraulic and mechanical milling chucks are prone to tool pullout in heavy metal removal applications.
This is why Haimer developed the Safe-Lock system, he says. Not only does it eliminate the risk of scrapped parts and broken tools, but it also allows shops to mill at higher depths of cut, feed rates and spindle speeds than with competing toolholding technologies. Similarly, the company also developed its Duo-Lock modular milling system (in conjunction with Kennametal), said to “more than double the metal removal rate as compared to existing modular systems in the market” in aerospace and other common milling applications.
“We designed both systems for aerospace shops that are machining large, very expensive blocks of metal, like airframe structural components,” Holden says.
“They’ve since become a no-brainer for this manufacturing segment, and for anyone else who wishes to maximize metal removal in milling applications where there are long depths of cut and large radial tool engagement.”
Cutting Tools
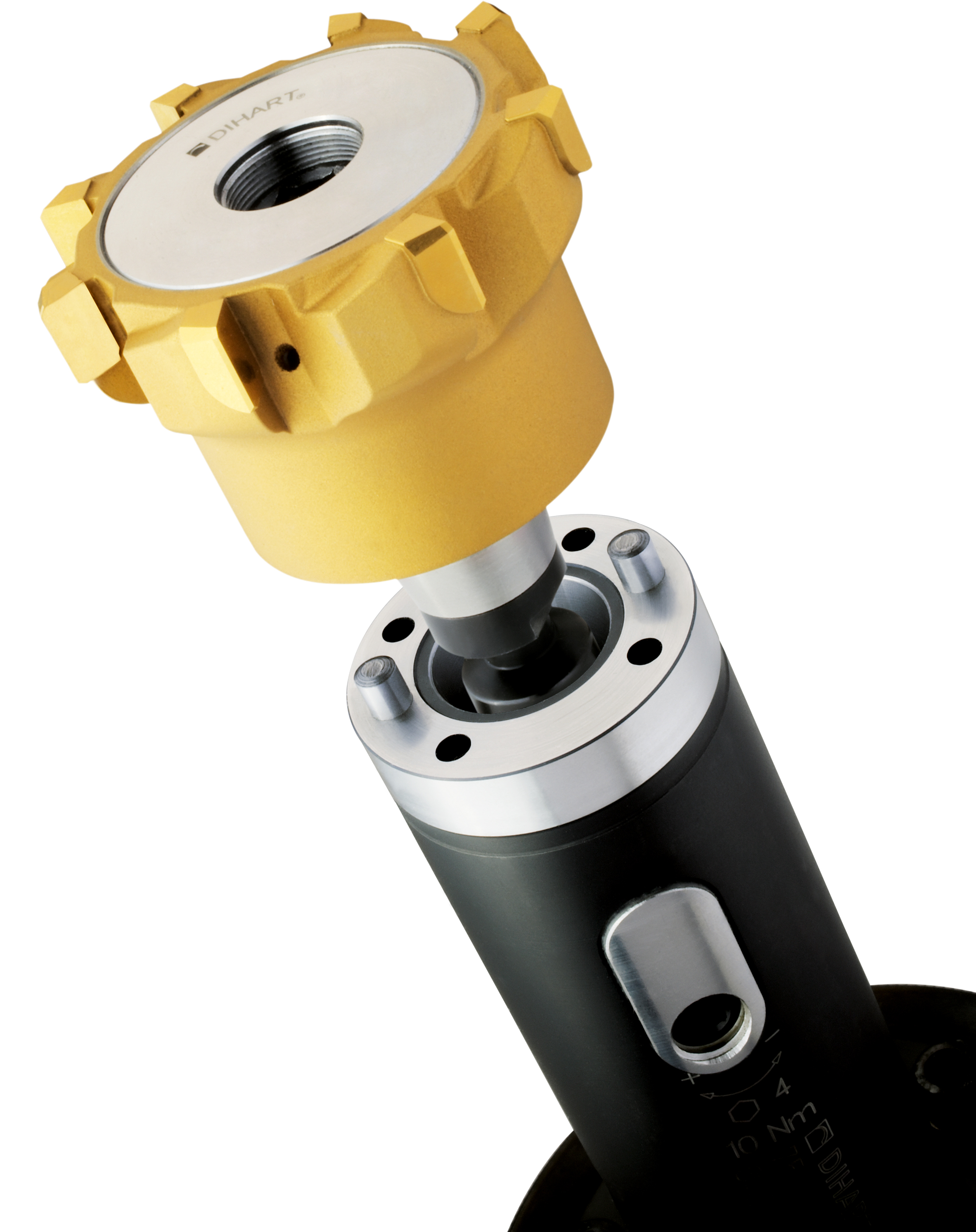
Ceratizit offers an extensive lineup of PCD milling, drilling and routing tools, cutters that are a must-have for shops that machine the composite materials just mentioned.
Mark Blosser, executive director of technology and solutions at Ceratizit, explains that the company’s aerospace offering goes far beyond cutting tools. He says the aerospace sector has ramped up quite quickly over recent months, and to meet specific demands, he and others within his group have developed special-purpose electronic boring tools that augment the capabilities of CNC equipment.
This technology is being applied to various complex internal bore machining that is seen in many aerospace components like braking components, landing gears and gear cases, he says.
“Instead of using special-purpose machines to cut the internal bottle-shaped features, they’re now putting them on machining centers that we’ve equipped with a wireless contouring and auto-compensating boring system. These U-axis heads allow them to do internal contouring and grooving, which means they can machine a complete part in one setup. It’s pretty cool stuff.”
Read more: 5 Ways Manufacturers Can Use Data Analytics to Improve Efficiency
Lasing Diamonds
Rick With, product manager and engineering supervisor for Guhring Inc.’s PCD/PCBN division, agrees with his colleagues on greater composite and titanium use within the aerospace industry but suggests that their lightweight counterpart aluminum isn’t going away anytime soon. Here again, PCD cutting tools are the first choice, especially for less machinable high Si (silicon) or 7075 aluminum where higher volumes or greater accuracy requirements are encountered.
One of the historical downsides of these brazed diamond tools, however, is the lack of chip formers and helix shapes, leading to less than optimal chip control. Guhring and others are addressing the second of these by applying diamond and diamond-like coatings (DLC) to solid carbide drills, end mills and reamers, greatly extending tool life when machining abrasive aluminum alloys or composite materials. They’ve also begun offering “veined” diamond tools and tooling with a solid PCD head that gives cutting tool manufacturers greater latitude in creating curved and helical geometries.
Another interesting development is the use of lasers to ablate chip formers in tools that would otherwise have a flat cutting face. “In the past, these tended to create long stringy chips that would wrap around the tool, leading to downtime and even part damage,” With says. “But new laser technology allows us to actually burn a chip breaker into the diamond itself, improving both chip manageability and part surface finish. It’s solved a lot of problems.”
What steps is your shop taking to capture the expected growth opportunities in aerospace? Let us know in the comments below.
Talk to Us!
Leave a reply
Your email address will not be published. Required fields are marked *