The next generation of grade: Tiger-tec® Gold
Walter AG, the Tübingen-based cutting tool manufacturer, is responsible for an important technological advance in the manufacturing sector. This machining specialist is one of the first companies in the world to present a new technology platform for coated indexable inserts based on CVD titanium aluminum nitride (TiAlN): Tiger·tec® Gold. In contrast to the cutting tool materials that have previously been used in the sector, Tiger·tec® Gold has significantly improved coating properties and therefore offers a considerably longer service life, increased process reliability, and increased productivity.
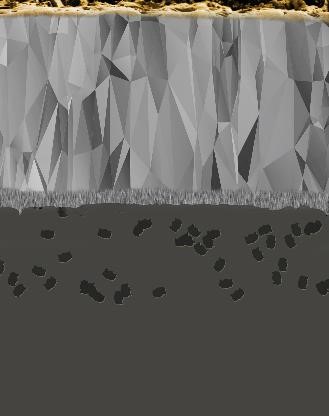
Global agreement over many years: For well over two decades, the machining sector has been working with CVD coatings that are based on aluminum oxide (Al2O3). The properties of these coatings were continuously improved throughout the years, but the developers have since reached their limits with this material. The technological options for further optimizing aluminum oxide grades have largely been exhausted now.
This was reason enough for the specialists at Walter to set about developing a new generation of grades for coating indexable inserts. The result: Tiger·tec® Gold – a completely new technological platform based on titanium aluminum nitride (TiAlN). Among other things, the coating impresses thanks to its extremely high hardness and residual compressive stress; it is ideal for milling steel and cast iron materials at medium to high cutting speeds.
Service life increased by around 80%
The developers at Walter have been using the new Tiger·tec® Gold WKP35G grade for some time now in special applications. In total, according to Jörg Drobniewski, Head of Cutting Material Development at Walter AG, they have carried out around 50 extensive test runs with customer applications since spring of this year. In doing so, the developers were able to prove that the coating properties had been significantly improved: The indexable inserts that were coated with Tiger·tec« Gold WKP35G stand out thanks to considerably higher wear resistance on flank faces, lower rate of hairline cracks forming and improved resistance to plastic deformation. But, above all: The practical tests showed that service life had been increased by around 80%.
Of course, this innovative leap is no accident. It was an important objective of the engineers at Walter to make the new generation of cutting tool material significantly more resistant to wear and, at the same time, process-reliable. The solution lies in a significantly higher aluminum content. The solution lies in a titanium aluminum nitride (TiAlN) with a significantly higher aluminum content of 85%, that is considerably above over the standard.
To achieve this, Walter developed a completely new process: The ULP-CVD technology. In a combination of ultra-low pressure (ULP) and chemical vapor deposition (CVD), the developers in Tübingen successfully separated TiAlN – the basis for manufacturing the new grades.
The door to new cutting material grades is pushed open
Jörg Drobniewski: "When developing Tiger·tec® Gold, we really had to think outside the box and move beyond the existing coating elements. In doing so, we entered uncharted territory and launched a completely new type of technology platform. We are convinced that, with this, we have opened the door to new cutting material grades for machining with carbide."
In addition to TiAlN as the main coating, the new WKP35G grade also uses titanium nitride (TiN). With its golden color, it also provides the name for this new coating technology from Walter.
Firstly, TiN is applied as a link between the carbide base substrate and the TiAlN main coating; secondly, it is used as the top layer above the main coating. "The golden color has the added welcome effect that it is now much easier to detect wear than it was in the past," explains Wolfgang Vötsch, Senior Product Manager for Milling at Walter. This guarantees optimum utilization of the cutting tool material – it is no longer the case that unused cutting edges are thrown away. The top TiN coating is textured. The indexable inserts that are coated with Tiger·tec® Gold are therefore ideal for machining cast iron.
Lower rate of hairline cracks forming
In addition to the significantly higher wear resistance on flank faces and the improved resistance to plastic deformation, which can all be attributed to the harder coating, Walter's new manufacturing procedure means that they have created yet another advantage: A lower tendency for hairline cracks to form. Jörg Drobniewski: "CVD coatings that are subjected to tensile residual stress have previously been commonplace across the sector. Our TiAlN coating is the first coating to be created in a CVD procedure that is subjected to compressive residual stress. This helps us to significantly minimize the formation of hairline cracks, and the cutting edge remains intact for longer – which is a prerequisite for a long, process-reliable service life."
The Head of Cutting Material Development is convinced that the new coating technology will really shake up the sector. Even more so than the fact that all practical tests with users in the automotive industry, in the energy sector and in general engineering sectors have confirmed the high expectations of his team. "We tested out a huge variety of scenarios – at cutting speeds between 120 m/min and 320 m/min, and workpieces made from various grades of steel and cast iron. The results were conclusive in all of the relevant parameters."
The advantages of Tiger·tec® Gold for the user can be summarized in four points:
- Significantly longer service life – 80% longer, on average
- Increased process reliability
- Increased productivity
- Optimum wear detection.
When the new generation of coatings is launched, Walter will offer the Tiger·tec® Gold WKP35G grade for milling steel and cast iron materials. Other grades will soon follow. At the start of 2017, the tool specialist wants to launch its first series of standard indexable inserts with the Tiger·tec® Gold coating on the market.
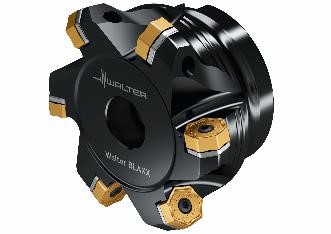
- Tiger-tec® Gold increases service life, 80% longer on average.
- Reliability and productivity are another advantage of the Tiger-tec® Gold technology.
- Walter's TiAIN coating is the first coating to be created in a CVD procedure that is subjected to compressive residual stress.
Talk to Us!
Leave a reply
Your email address will not be published. Required fields are marked *