More than a century of expertise in cutting tool manufacturing, combined with powerful R&D resources, place Guhring at the forefront of technical innovations in cutting tools. Guhring meets specific customer requirements—from process proposal to production application—with quality cutting tool solutions. With approximately 8,000 employees across the globe, and more than 70 production locations in 48 countries, Guhring is a powerful metalworking resource.
Fluteless taps, or roll form taps, are used for the forming of internal threads without chip removal. In contrast to conventional tapping where material is cut from the workpiece, thread forming is a pressure deformation process without chip removal for the production of internal threads. During the process, the material is cold formed or pressed into thread geometry without interrupting the grain flow. As a result, the threads formed by this pressure deformation are stronger than those from a cut tap.
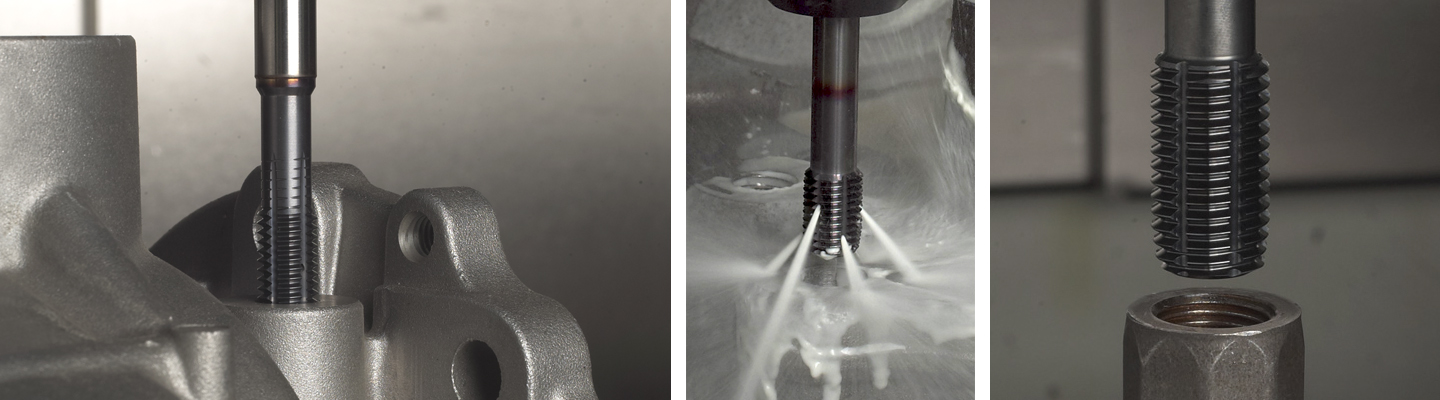
There are several advantages to thread forming:
- No chip is produced, therefore there are no chip evacuation or bird nesting problems, regardless of depth of threaded hole.
- One tool can be used for the production of threads in through and blind holes.
- Applications in wide range of materials are possible with the same tool.
- Pitch and angle of thread errors that can occur with thread cutting are eliminated.
- Internal threads produced by thread forming possess a higher tensile strength thanks to the uninterrupted grain flow and the cold forming process.
- The surface finish of the thread is superior.
- Fluteless taps can be applied at higher speeds because the formability of many materials increases with the forming speed. This does not have a negative effect on the tool life.
- Reduced danger of breakage due to the rigid design of the tap.
Notes of caution before selecting a form tap:
- Workpiece must be a ductile (formable) material.
- The part must have a wall thickness that will prevent the external dimensions from deforming while the internal thread is being formed.
- Tapping hole size optimization is key to managing minor thread diameter after forming, torque, tool life and process reliability.
- Lubrication is especially important in thread forming (preferably 10% water soluble or greater), to prevent build-up of material and excessive torque.
If you are able to manage the above mentioned factors, using pressure deformation to create threads can reward with great versatility, improved productivity and extended tool life in a vast range of applications. The design of the form tap can have a big influence on your potential for success and your ability to avoid the pitfalls. There are several features of new Pionex® taps from Guhring that make it easier to choose thread forming for your application.
Talk to Us!
Leave a reply
Your email address will not be published. Required fields are marked *