The goal in solid carbide drilling is to obtain a balanced wear across the drill’s cutting edge. Uneven tool wear indicates a problem in the drilling process that can result in shorter tool life, tool breakage and damaged components. In this video, Sandvik demonstrates how to identify tool wear problems and workpiece errors when using solid carbide drills.
For a full transcript of the video, click here
In this video, Sandvik demonstrates how to identify tool wear problems and workpiece errors when using solid carbide drills.
Video Transcript
The goal in solid carbide drilling is to obtain balanced wear across the drill's cutting edge. Uneven tool wear indicates there's a problem in the drilling process that can lead to shorter tool life, tool breakage or damaged components.
In this film we will demonstrate how to identify and rectify tool problems and workpiece errors when using solid carbide drills. Stability in your tooling setup promotes excellent chip control and an even flank and crater wear to the cutting zone. Good chip formation and evacuation is essential to a successful drilling operation. The workpiece material, choice of drill, coolant pressure and volume and cutting data are all important considerations. Chip jamming can cause radial movement of the drill and affect hole quality, drill life and reliability.
Chip formation is acceptable when chips can be evacuated from the drill without disturbance. The start chip from entry into the workpiece is always long and does not create any problems. Chips are formed from the centre to the outer corner of the drill. Examine the chips. If they are long and bent instead of curled, this means that chip jamming has occurred. Examine the hole. If chip jamming has occurred, an uneven surface will be visible. The best way to identify excessive tool wear is to listen during drilling. A consistent sound indicates good chip evacuation. But an interrupted sound typically means there is chip jamming.
In addition to poor chip control, there are a number of other factors that could indicate excessive tool wear, including a rise in machine power, increased exit burr, excessive heat or noise generation and of course tool breakage. When examining a solid carbide drill, note that there are many different types of tool wear. A built-up edge can be caused by any of a number of factors. You can avoid this condition by increasing the cutting speed, using a coated drill with sharper cutting edge and using an external cutting fluid with a good percentage of oil.
Chipping on the edge corner can be prevented by carefully monitoring your operation. Check to make sure the fixturing and tool holder are stable. Check radial run-out and the cutting fluid supply. You may also need to decrease the feed rate.
Another common issue is large wear on the cutting edge. You can prevent this by decreasing cutting speed, increasing the feed rate or changing to a harder grade. It may also be necessary to increase the fluid supply. Chipping on the cutting edge may also lead to operational problems. Avoid this by checking the setup for unstable conditions and making sure you don't wait too long to replace the drill. If allowable wear is exceeded, you can damage your workpiece.
Wear on circular lands can be prevented by checking the radial run-out, decreasing the cutting speed or changing to a harder grade. In some cases it may be necessary to strengthen the cutting fluid with neat oil or stronger emulsion. Production issues can also be caused by wear on the chisel edge. Increasing the cutting speed or decreasing the feed rate should prevent this from happening. You should also check the drill dimensions to ensure the chisel edge is within manufacturing specifications.
To learn more about solid carbide drills, visit the Sandvik Coromant website or go to MSCDirect.com to see the full line of products from this supplier.
Brought To You By
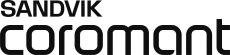
Sandvik Coromant is the world’s leading supplier of tools, tooling solutions and know-how to the metalworking industry. With extensive investments in research and development they create unique innovations and set new productivity standards together with their customers. These include the world's major automotive, aerospace and energy industries.
Related Articles
In this episode of MSC Industrial Supply's "How To," host Jacob Sanchez explores the cutting-edge world of tooling and machining innovation with Mitsubishi Materials.
Join Jacob Sanchez in this episode of MSC Industrial Supply's "How To" series as he explores how Walter America builds strategic partnerships beyond traditional supplier relationships.
HAIMER details the key characteristics of each of their balancing machines to help operators select the right one.
Talk to Us!
Leave a reply
Your email address will not be published. Required fields are marked *