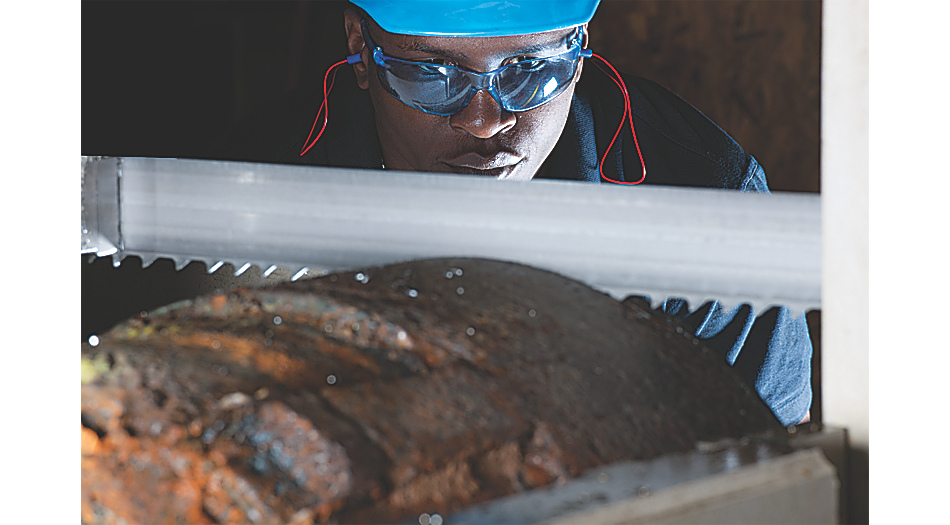
As end markets like aerospace and medical look for ways to improve the strength and reliability of their products, many machine shops are seeing increased use of harder materials like titanium alloys.
However, there are a few characteristics that make titanium alloys more challenging to work with than many other metal materials. To help machine shops tackle this often tough-to-cut metal, the following is a brief overview on titanium alloys and the most effective cutting tools and methods for working with this material.
Taking on Titanium
Titanium alloys are praised for their strong, yet lightweight properties. The material also has outstanding corrosion resistance. As explained here by Modern Machine Shop, these properties make the material an ideal choice for aircraft designs, medical devices, and implants.
However, titanium can be tricky to work with due to its reactivity at higher temperatures and its tough composition. “Since titanium’s heat conductivity is low, it will flex and return to its original shape a lot more easily than steel or high-nickel alloys,” explains an article from American Machinist. “The downside of this is experienced during machining: the heat from the operation does not transfer into the part itself or dissipate from the tool edge, which can shorten tool life.”
The article goes on to say that this issue is compounded by the tight tolerances demanded by most customers. “For aerospace, the tolerances are to within a thousandth of an inch, and if violated, the part must be scrapped,” the article states. “Achieving such tolerances while using such a malleable material is difficult, and wear on the cutters increases significantly compared to similar efforts with nickel and chromium alloys.”
The technical article, “Machining Titanium and Its Alloys,” published by jobshop.com provides key insights into the chemistry behind titanium alloys and lends the following tips for its successful manufacturing:
- Use low cutting speeds
- Maintain high feed rates
- Use generous amounts of cutting fluid
- Use sharp tools and replace them at the first sign of wear, or as determined by production/cost considerations
- Never stop feeding while a tool and a work piece are in moving contact
Choosing the Right Blade
Like any material, one crucial aspect of cutting titanium alloys is choosing the right tool. As industry experts, The LENOX Institute of Technology (LIT) offers critical advice concerning blade selection in its white paper, Characteristics of a Carbide-Friendly Bandsaw Machine. Since titanium alloys are a stronger and harder material, they pose a unique cutting challenge best solved by carbide blades. Using a carbide-tipped band saw blade not only allows for the successful cutting of titanium alloys, but it simultaneously offers longer blade life and faster cutting as well.
LIT’s white paper further elaborates on the benefits of the carbide technology by providing a real-life comparison between a bi-metal and a carbide blade. The test produced the following results:
- The bi-metal band saw blade (Contestor GT) ran 120 feet per minute with a feed rate of 0.53 inches per minute.
- The carbide blade (Armor CT Black) ran at 320 feet per minute with a feed rate of 3.11 inches per minute.
Ultimately, the higher speed and feed rate of the carbide blade enabled it to make the cut 13 minutes faster, translating into 160 more parts produced during an 8-hour shift than its bi-metal counterpart.
Meeting Material Demands
Material trends will come and go, but metal-cutting companies that want to successfully serve existing and potential customers need to be prepared to adapt to the industry’s changing material needs. As the use of titanium grows, today’s machine shops need to understand the material’s unique characteristics and machining requirements so they are fully equipped to tackle every one of their customers’ demands.
- Titanium alloys are strong, yet lightweight and has outstanding corrosion resistance.
- Since titanium’s heat conductivity is low, it will flex and return to its original shape a lot more easily than steel or high-nickel alloys.
- Metal-cutting companies that want to successfully serve existing and potential customers need to be prepared to adapt to the industry’s changing material needs.
Previously featured on Blog.LenoxTools.com.
Talk to Us!
The above short article appears to have been written by someone with little or no actual experience in machining titanium. The machining tips are much the same as for 300 series SST; relatively slow speed, relatively high feed rate, lots of coolant, and do not let the tool rub on the titanium while not feeding etc. MSC is a great company, but they should not let amateurs write about technical things they know little or nothing about. Suggest the writer stick with what they know and not waste my time with amateur articles!
28Thanks, Bert for weighing in.
29Leave a reply
Your email address will not be published. Required fields are marked *