Kennametal delivers productivity to customers seeking peak performance in demanding environments by providing innovative custom and standard wear-resistant solutions, enabled through our advanced materials sciences, application knowledge, and commitment to a sustainable environment.
You know from experience that while composite layers are strong, they also can wear down a tool’s geometry in a matter of minutes and splinter at the edge when machined. Such splintering causes weakness. You don’t want splintering on an aircraft hull or wing. Kennametal has created a tool with the right geometry, clearance, and coating to withstand composite wear and eliminate splintering.
Carbon-fiber reinforced polymer (CFRP) is a popular composite material that has the right mix of weight-to-strength ratio, durability, and extreme corrosion resistance. This makes it well suited for aircraft hulls and wings.
But you know from experience that while composite layers are strong, they also can wear down a tool’s geometry in a matter of minutes and splinter at the edge when machined. Such splintering causes weakness. You don’t want splintering on an aircraft hull or wing.
Your challenge: Find a tool with the right geometry, clearance, and coating to withstand composite wear and eliminate splintering.
Kennametal's solutions: Kennametal tungsten carbide grade KCN05™ with diamond coating for routers and SPF drills. The diamond coating of grade KCN05 preserves the geometry through the cut, so you get consistent, clean edges and finishing. Kennametal SPF drills have been shown to last up to 10 times longer than uncoated solid carbide drills in CFRP applications. Their KCN05 routers are available in down-cut, compression, burr, and ball-nose styles and designed for smooth finishing in CFRP.
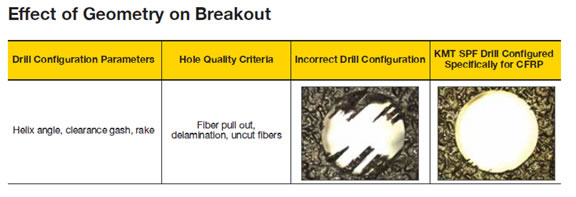
To view the full line of products from Kennametal, visit MSCDirect.com.
Brought To You By

More from Kennametal
More on Aerospace
Castrol and Fort Walton teamed up to run trials and receive the OEM approval for Hysol SL 45 XBB.
In automated machining for aerospace, one particular challenge is deburring the intersection of cross-drilled holes frequently found in engine components.
Fort Walton sponsored Castrol to get approval from a major aerospace OEM using Hysol SL 45 XBB.
Talk to Us!
Leave a reply
Your email address will not be published. Required fields are marked *