What does it take to make parts for precision manufacturing? What is it like to be a small manufacturer for medical parts? We explore the opportunities with a fresh perspective from a Michigan-based company doing it today: Rocket Machining & Design.
Precision manufacturing is big business—especially in medical manufacturing. In the U.S., the market is expected to reach $173 billion in 2019, according to medical device consulting firm Emergo. Small- to medium-sized job shops looking for new markets might find a good fit in the lucrative medical supplies and devices market. But with the opportunity there are challenges in the types of equipment and skills required to compete for jobs manufacturing these small, complex parts.
One example of a successful entry into precision medical parts manufacturing is Rocket Machining & Design, which opened its doors on Dec. 17, 2017, and completed its first part on Jan. 31, 2018.
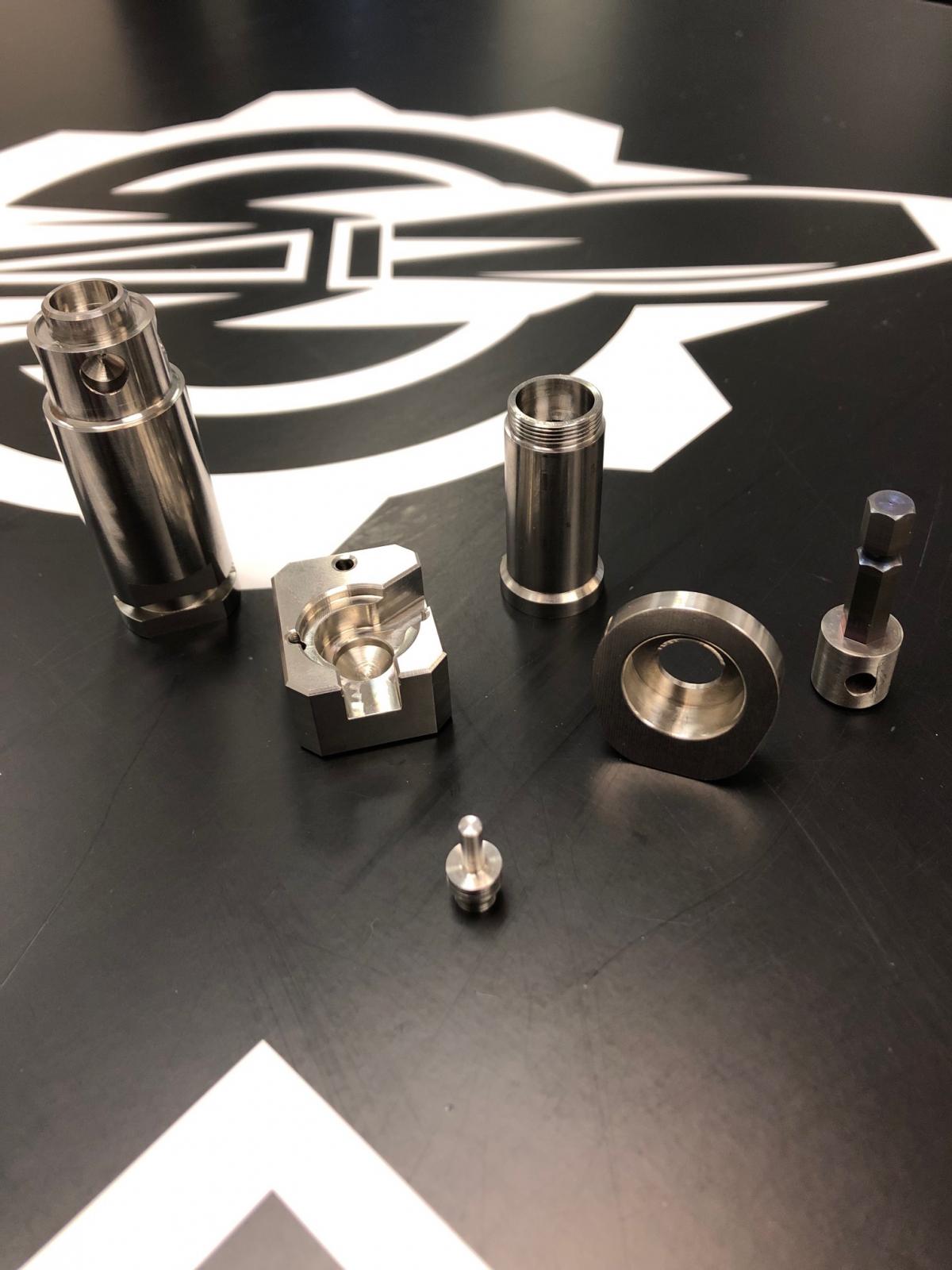
Located in Springfield, Michigan, Rocket Machining & Design is not far from Kalamazoo, headquarters of medical device giant Stryker (see sidebar). Though Rocket started out in other types of machining work including automotive, energy and fluids, the company was soon introduced to Stryker through its MSC representative.
“It’s been a great relationship, and recently we’ve grown and taken over a lot more of Stryker’s work,” says Duane Spurling Jr., managing partner for Rocket Machining.
Many of the parts Rocket Machining & Design is making are components and prototypes for surgical instruments.
The Types of Machines Needed for Medical Parts Manufacturing
For its medical work, Rocket uses Haas CNC machines, including a TL-1 and an ST-30, as well as Haas mills and a surface grinder.
“Currently we’re turning the medical parts and then putting them in the mill, or vice versa, which has been kind of rough,” says Spurling.
“Now that we’re seeing more of these parts come through, we know it’s important for us to get a machine that’s done-in-one production, so we are actually in the process of purchasing a live tooling lathe, maybe a Haas ST that can handle barstock up to 20 mm wide,” he says.
Need to know the preferred techniques for working with medical-grade titanium, cobalt chrome and nickel-based stainless-steel alloy? Read “8 Must-Know Tactics for Precision Medical Machining.”
Talk to Us!
We have a cc lacer
191Thank you very much for sharing these ideas. I really appreciate your efforts for creating this exceptionally well content. I was looking for such content about precision manufacturing, journey making medical equipment parts, you have really helped me with the same, great post!! Check our industrial vacuums
192Thank you very much for sharing these ideas… I really appreciate your efforts in creating this exceptionally good content. I was looking for such content about journey making medical equipment parts, you have really helped me with the same… great post!! For more info about us, visit https://www.fuson-cncmachining.com/
189Your article is quite helpful! I have so many questions, and you have answered many. Thank you! Such a nice and superb article, we have been looking for this information about precision manufacturing one shop. Great post…
197Thank you, we are very glad you found this information useful!
192It is a nice article about three reasons about digital preservation framework released for public comment. I agree with all your points that you have stated here, love this blog. Check our Vacuum Pumps
188Hi, thank you for such a brilliant post. I have been reading some blogs that gives me more knowledge about this topic on precision manufacturing one shop’s journey in making medical equipment parts. I must say this is one of the best among them. You have done a great research for I feel, thanks for sharing.https://www.fuson-cncmachining.com/
197Your article is quite helpful! I have so many questions, and you have answered many. Thank you! Such a nice and superb article, we have been looking for this information about journey making medical equipment parts Great post…
https://primepump.co.nz/products/food-beverage/
194Leave a reply
Your email address will not be published. Required fields are marked *