This challenging material makes unique demands on cutting tools, but a combination of R&D, lab tests and the results of real world applications is leading to effective solutions.
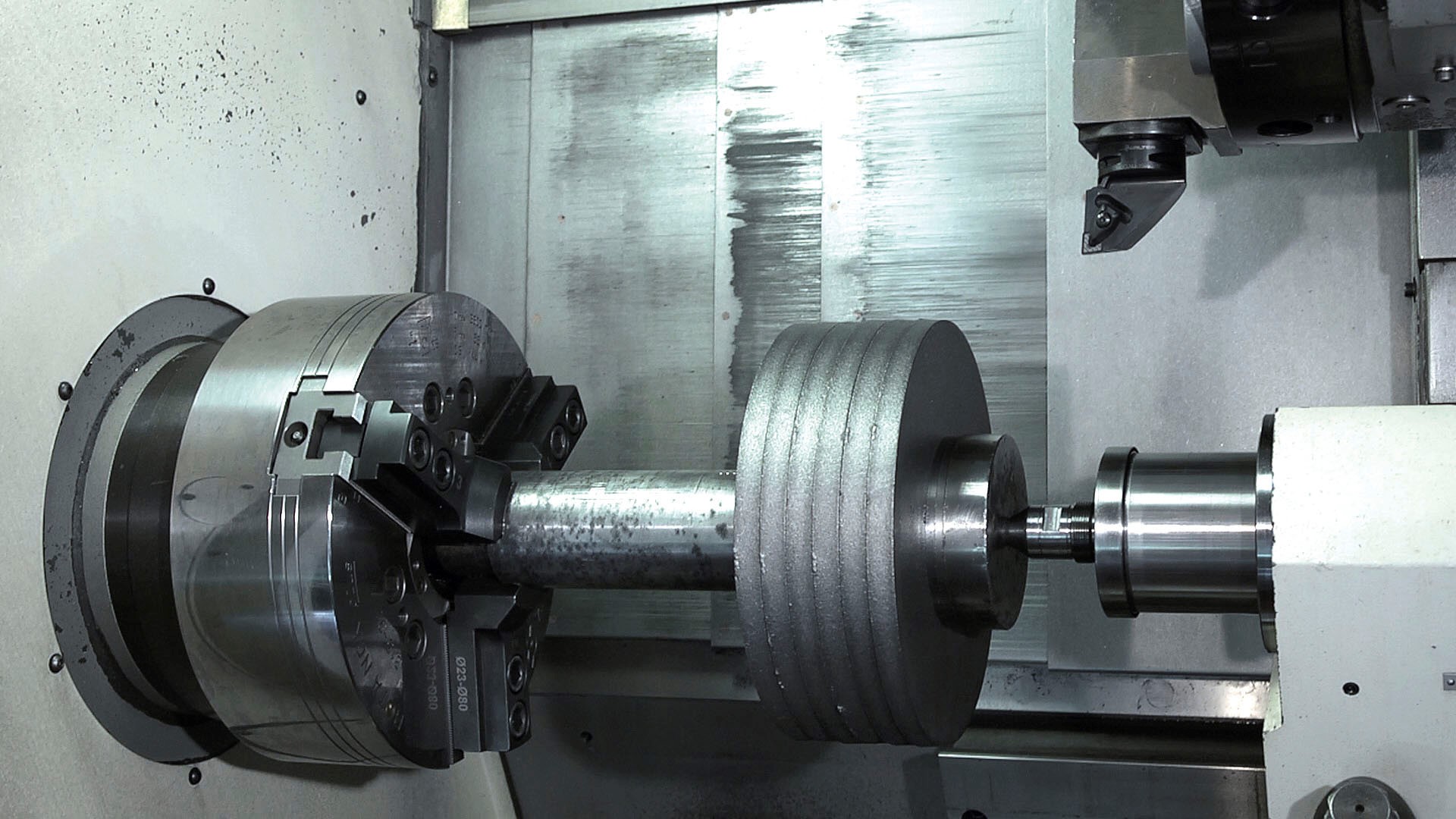
Cast iron remains one of the toughest materials to machine. That’s primarily because it has inconsistencies in its composition and its structure varies, particularly on the outer surface. This leads to significant variations in machinability. Interrupted cuts or unstable machine conditions may also have to be taken into consideration when machining cast iron. These factors are particularly challenging for the cutting tools, especially for roughing tools used in high volume production, where tool life and process reliability have a large influence on costs.
Cast iron is still heavily used, despite the increased use of light metal alloys. The rise of light metal alloys means, for example, that the engine blocks in small and medium-sized cars today are often made from aluminum. However, in larger cars with bigger engines of around two liters or more, aluminum engine blocks would need to be considerably larger. In this case cast iron allows for thinner walls and a more compact engine. This is an important factor particularly for transversely mounted car engines.
The question of "cast iron or aluminum" does not apply to diesel engines or commercial vehicles. In this area, there is no competition because of the vibration dampening effects of cast iron, normally in the form of compacted graphite cast iron. Its strength lies between that of gray iron and ductile iron.
"Cast iron machining is a very important application area for us," says Gerd Kussmaul, senior product manager for turning at Walter. It’s a sentiment shared by other leading tooling companies, especially in recent years, as the auto industry has pushed for more efficient and reliable ways to machine this vital but difficult material. “Within it we have several focus sectors, such as the automotive industry, general industry and construction, with components such as engine blocks, wheel hubs, pumps, and differential or gearbox housings," he added.
The use of cast iron to permit thinner engine walls was mentioned earlier. Machining these thinner walls, however, typically induces vibration. That’s why tools that are both soft-cutting and sturdy are needed. To attain that mix these tools need to have certain characteristics, the first of which is a high performance coating. Why?
"The coating must have an optimized microstructure that enables increased thermal wear resistance, and provides maximum tool life and cutting speeds,” he answers. “In addition, a special surface treatment which converts the tensile stresses in the coating into compressive stresses.” This is designed to increase the toughness of the cutting tool material, which boosts reliability of the cutting edge, particularly when machining cast scale. Both the wear resistance and toughness are therefore greater than with conventional coatings.
Kussmaul stresses that the proper insert geometry is also crucial as the macro and microgeometry of a cutting edge have a significant influence on chip formation and, therefore, on the resulting cutting forces. Choosing the right geometry for the application, preferably one with a ground contact surface to ensure secure seating of the indexable insert, is crucial. "An advanced coating together with the optimized geometries and today’s new cutting tool material grades can lead to maximum cutting performance and an increase in tool life of up to 75 per cent," he says.
Multiple edges for milling
Perhaps the majority of workpieces encountered in cast iron machining, and generally also the largest, are cubic in shape and are therefore a job for a milling machine or machining center. One of the most common operations is the face milling of sealing and attachment surfaces, such as cylinder head surfaces on engine blocks.
“In the automotive industry, it is important to process as many surfaces as possible in the shortest time and with process reliability. Large milling cutters with multiple cutting edges are required for the appropriate metal removal rates,” says Wolfgang Vötsch, milling specialist in product management at Walter.
Vötsch points to his company’s F4045 as a prime example of the type of tool required to maximize cast iron machining productivity and process reliability. The F4045’s inserts provide 14 useable cutting edges because the symmetrical indexable inserts are not only indexed radially, but also reversible. These characteristics make for a highly efficient cast iron cutter, which drives down cutting edge costs. In addition, a positive overall geometry provides low cutting forces and reduced power consumption.
Another desirable feature in a milling cutter is an insert wedge clamping system so that the indexable insert can be fitted precisely and securely in its seat. With this design the clamping wedge pivots to the side after just a few turns of the clamping screw to enable quick and easy access to the indexable insert.
"Handling is of crucial importance for a tool with many useable cutting edges," explains Vötsch. "If the indexable inserts cannot be turned around or indexed quickly and easily by hand, much valuable time is lost."

- Cast iron is still heavily used, despite the increased use of light metal alloys.
- Larger cars with bigger engines of around two liters or more, cast iron allows for thinner walls and a more compact engine.
- Machining thinner walls, typically induces vibration. That’s why tools that are both soft-cutting and sturdy are needed.
Talk to Us!
I could really use something that can do interrupted cast iron cutting with a light weight 8" face mill.
35Leave a reply
Your email address will not be published. Required fields are marked *