Sandvik Coromant is the world’s leading supplier of tools, tooling solutions and know-how to the metalworking industry. With extensive investments in research and development they create unique innovations and set new productivity standards together with their customers. These include the world's major automotive, aerospace and energy industries.
Machining parts at 50 HRc or more has traditionally been done by dedicated grinding equipment and processes.
Machining parts at 50 HRc or more has traditionally been done by dedicated grinding equipment and processes. However, with advances in technology both in the capability of machines such as turning centers, but also in the grades and geometries of dedicated inserts which offer predictable wear development, more parts per insert used and, of course, the speed of production; all resulting in lower cost per component.
Machining components from hardened materials have proven to be difficult given several requirements such as stability-demanding setups, abrasive materials resulting in greater wear and heat generated as well as greater cutting forces applied to the cutting tools. However, the benefit lies in reducing machining time and costs by 70% or more offering improved lead times and higher quality of the component produced.
Typical parts include brake rotors, transmission gears, steering pinions, valve seats, pistons, cylinder liners and clutch housings.
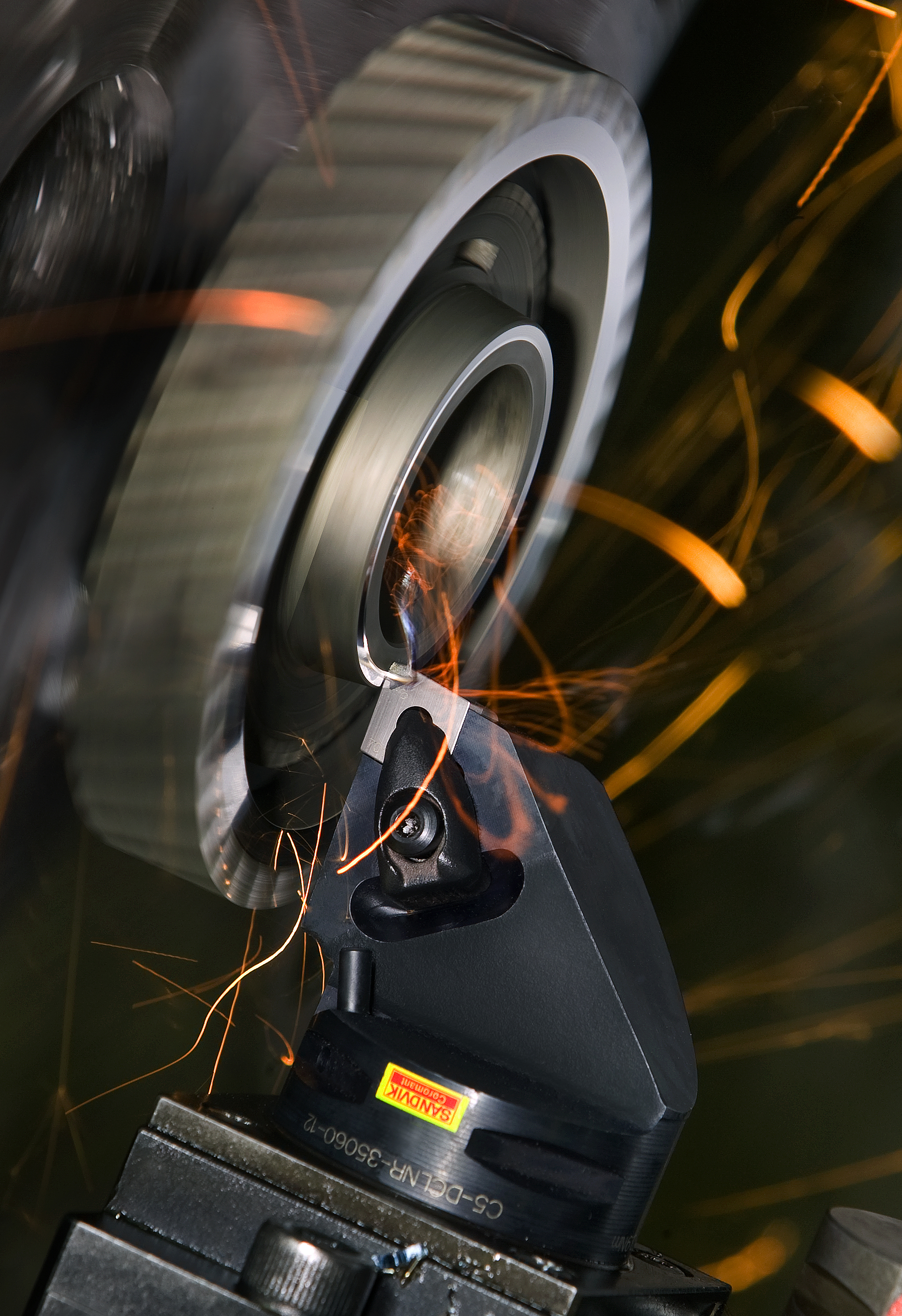
Superior Surface Finish
Hard part turning applications demand high dimensional accuracy and surface quality. The CoroCut 1-2 insert allows for very high feed rates without compromising surface finish. Yet, it is still able to meet the closest surface and dimensional tolerance requirements. Achieving productivity targets when manufacturing automotive transmission components has now become significantly easier. The new -XB geometry features a special grinded edge profile that allows for machining at very high feed rates, up to 0.0047 in/rev (1.2 mm/rev). This results in higher productivity for longitudinal and face hard part turning.
If the conditions are stable, always use wiper geometry for best productivity. For semi-finishing, use WG geometry and for finishing, use WH geometry. A normal radius insert should be used only when stability is poor, such as slender workpieces.
Key Factors in Hard Part Turning
In addition to the general recommendations for turning, there are some more specific factors that should be highlighted when machining materials over 50 HRc. When preparing the workpiece in the soft stage, ensure that you:
- Avoid burrs
- Maintain close dimensional tolerances
- Chamfer and produce radii in the soft stage
- Do not enter or leave cuts abruptly
- Enter or leave cuts by rolling into or out of cut
Setup and Machine Stability
Clamping and alignment of the workpiece are crucial for machine stability. As a general guideline, a workpiece length-to-diameter ratio of up to 2:1 is normally acceptable for workpieces that are only supported on one end. If there is additional tailstock support, this ratio can be extended. During your setup, note that a thermally symmetrical headstock and tailstock design will add extra dimensional stability. For excellent tooling stability, use the Coromant Capto modular quick change tooling concept. The Coromant Capto and QS holding systems help you maximize your productivity while Silent Tools reduce vibration and enable machining of long overhangs. For internal turning, consider carbide shank boring bars and Silent Tools for improved stability and surface finish. With the CoroTurn SL modular system, you can also build customized tools for a variety of machining applications.
Coolant and Wear
Hard part turning without coolant is the ideal situation and is entirely feasible. Both CBN and ceramic inserts tolerate high cutting temperatures, which eliminate the costs and difficulties associated with coolants. Some applications may require coolant, such as situations when controlling the thermal stability of the workpiece. In these cases, ensure a continuous flow of coolant throughout the entire turning operation. Generally, the heat generated when machining is distributed into the chip (80%), workpiece (10%), and insert (10%).
High heat in the cutting-edge zone reduces the cutting forces. Therefore, a cutting speed that is too low generates less heat and can cause insert breakage. Crater wear gradually affects the insert strength, but does not affect the surface finish to the same degree. In contrast, flank wear gradually affects the dimensional tolerance.
Strategies
In hard part turning, you can choose to implement either a one-cut or two-cut strategy. A one-cut metal removal strategy is feasible for both external and internal operations. A stable setup is always important and the tool overhang should not exceed the bar diameter in internal turning (1xD). For good machining, we recommend chamfered, lightly-honed inserts (S-type), and moderate speed and feed. The advantages here are the quickest possible machining time and one tool position. The disadvantages, however, include difficulties in meeting stringent dimensional tolerances, shorter tool life (than two-cut) and tolerance deviations due to relatively rapid wear.
A two-cut strategy allows unattended machining of high-quality finished surfaces. Recommended are roughing inserts in S-type, with a 0.047 inch (1.2 mm) radius, and the finishing inserts with a chamfer only (T-type). Both inserts should have wiper geometry to ensure the high-quality surface finish. The advantages here include tooling selection optimized for roughing and finishing, and higher security, closer tolerances and potentially longer runs between tool changes. The disadvantages include one extra tool change and the need for two tool positions in the machine.
It is recommended you always consult with your Sandvik Coromant Sales Representative when selecting tooling and machining strategies for your production requirements.
Previously featured on Sandvik Coromant's website.
Brought To You By
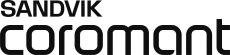
More from Sandvik Coromant
More on How-to
Toolholders are the most important connection between the machine and cutting tool. High-quality toolholders can extend tool life and save you money.
In this episode of MSC Industrial Supply's "How To," host Jacob Sanchez explores the cutting-edge world of tooling and machining innovation with Mitsubishi Materials.
In pipeline construction, properly preparing and cleaning the base material is the first step toward ensuring quality welds and minimizing defects.
Talk to Us!
That is really cool that I should consider carbide inserts for internal turning. That is something that I would want to have if I were in the industrial cutting business. That is something that I am sure someone would want to have for internal cutting needs. http://olsoncarbide.com/product-applications/
23Leave a reply
Your email address will not be published. Required fields are marked *