Kennametal delivers productivity to customers seeking peak performance in demanding environments by providing innovative custom and standard wear-resistant solutions, enabled through our advanced materials sciences, application knowledge, and commitment to a sustainable environment.
Most advanced turning grade is the new champion for machining nickel, cobalt and iron-based metals for aerospace and beyond.
Kennametal has introduced its newest and most advanced turning grade, KCS10B, for nickel, cobalt and iron-based superalloys used in aerospace and other high-temperature applications.
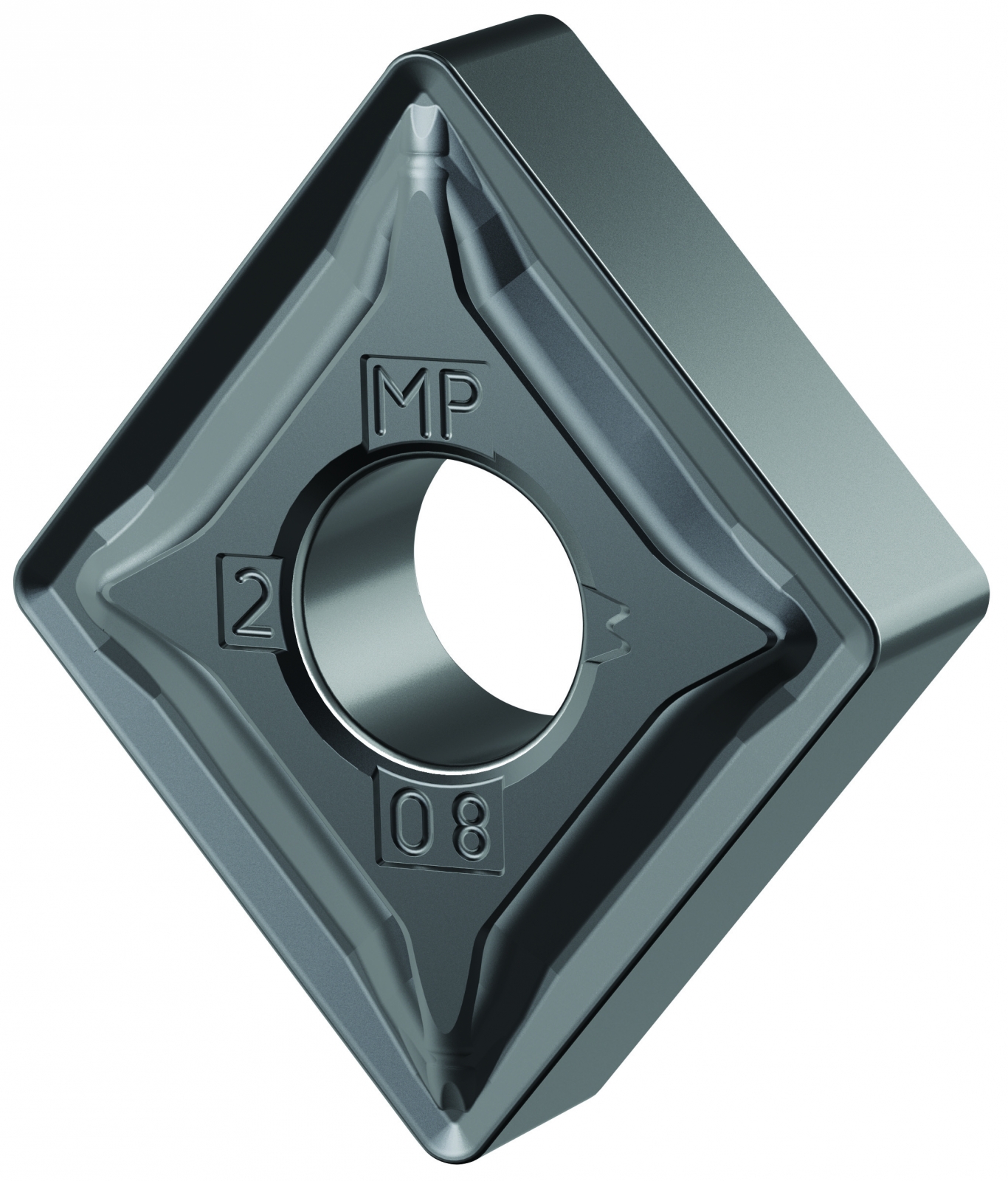
turning insert shapes, sizes and geometries
KCS10B, which features a revolutionary coating applied to an ultra-fine grain carbide substrate for superior layer adhesion, delivers up to 50% greater tool life, more predictable processes, and improved productivity when working with difficult-to-machine superalloys. KCS10B overcomes the most common challenges encountered in turning superalloys—cratering and depth-of-cut notching—two wear modes that often lead to unexpected and even catastrophic tool failure.
Talk to Us!
Leave a reply
Your email address will not be published. Required fields are marked *