Sandvik Coromant is the world’s leading supplier of tools, tooling solutions and know-how to the metalworking industry. With extensive investments in research and development they create unique innovations and set new productivity standards together with their customers. These include the world's major automotive, aerospace and energy industries.
The use of coolant and lubrication has a large impact on process security in many metal cutting applications.
The use of coolant and lubrication has a large impact on process security in many metal cutting applications. If applied right, it reduces temperature at the cutting edge and improves chip evacuation.
From an environmental and manufacturing cost perspective, dry machining is best. However, many applications require coolant for tolerance, surface and machinability. If coolant is required, then it should be optimized to maximize the potential.
The benefits can be great for turning operations, however:
Tools developed for high precision coolant applications – i.e. turning tools with targeted jets – are strongly recommended for finishing applications.
- The coolant pressure required to break the chip for turning tools is dependent upon the nozzle diameter (outlet), material being machined and the depth of cut and feed.
- The coolant flow required is dependent upon the pressure and the total coolant delivery area of the coolant holes.
- In medium and roughing applications, it is recommended to use under coolant whenever possible. The under coolant controls the heat in the cutting zone which leads to improved tool life and predictable machining. For finishing operations, it is recommended to use both high precision coolant as well as under coolant.
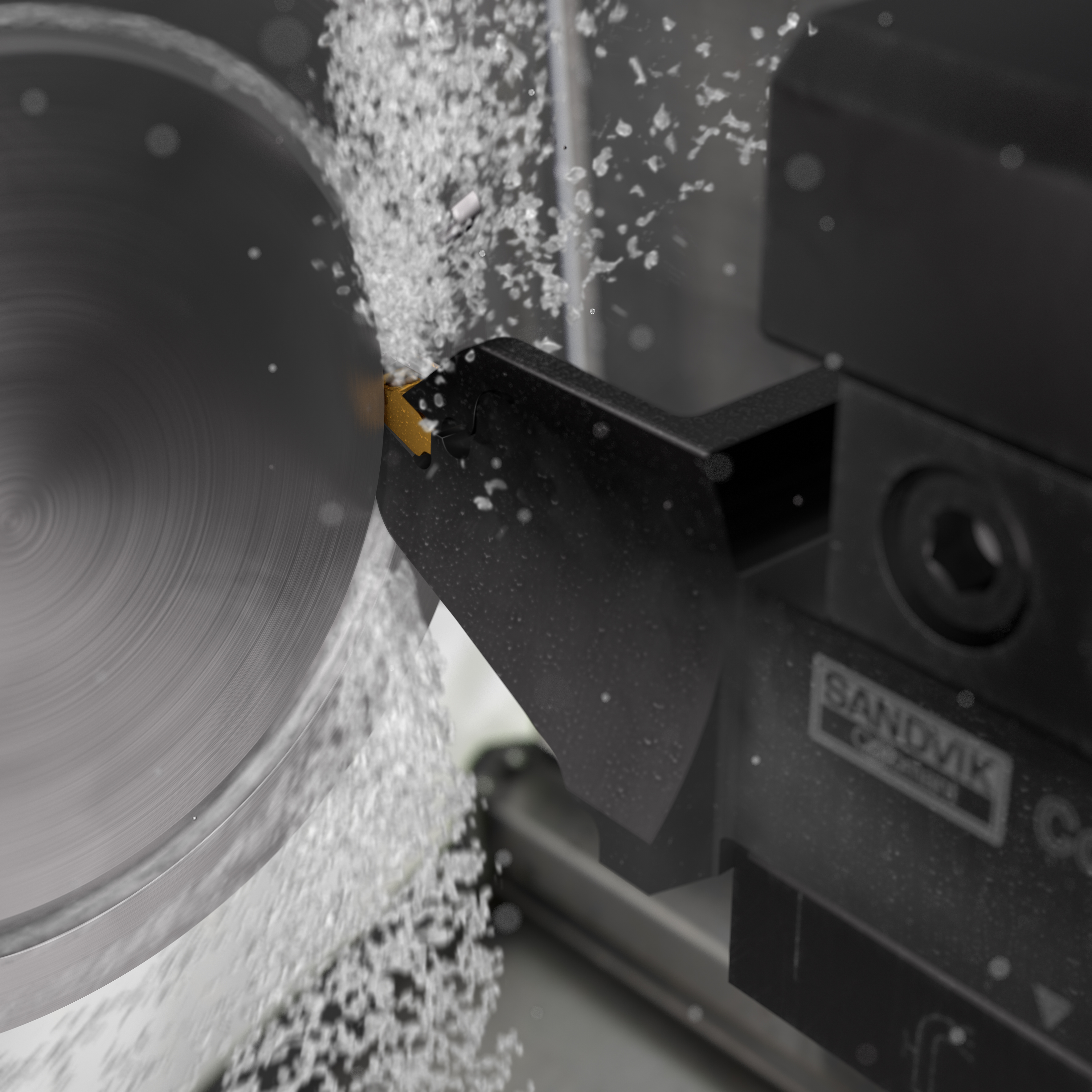
Correctly applied coolant will improve the tool performance and component quality. Modern turning tools feature nozzles that deliver high precision coolant from above which controls the chip breaking for secure machining. More advanced tools feature also under coolant which controls the temperature for long and predictable tool life.
Traditionally, coolant has either been applied externally or internally directed solely at the topline cutting edge. When external coolant is applied, normally the amount of coolant that gets into the cutting edge heat zone is very limited. With internal coolant, the coolant ports access the cutting edge and the workpiece, improving edge security and consistency in performance.
Over and under coolant. When to use what?
Depending on your machining conditions, you can choose to apply tools with internal over and under coolant. Sometimes you just need one of the options, but you get the best effect by using both at the same time. Over coolant improves chip control, which is the key to long tool life and few machine stoppages. Coolant from above can also reduce build-up edge. Under coolant reduces temperature and at the same time flank wear. It also improves chip evacuation and reduces cutting edge temperature, allowing for the use of softer insert grades with maintained or sometimes increased tool life and cutting data. In combination with softer grades, it also adds more predictable and secure machining processes. Under coolant gives large gains in long cuts where temperature often is a limiting factor.
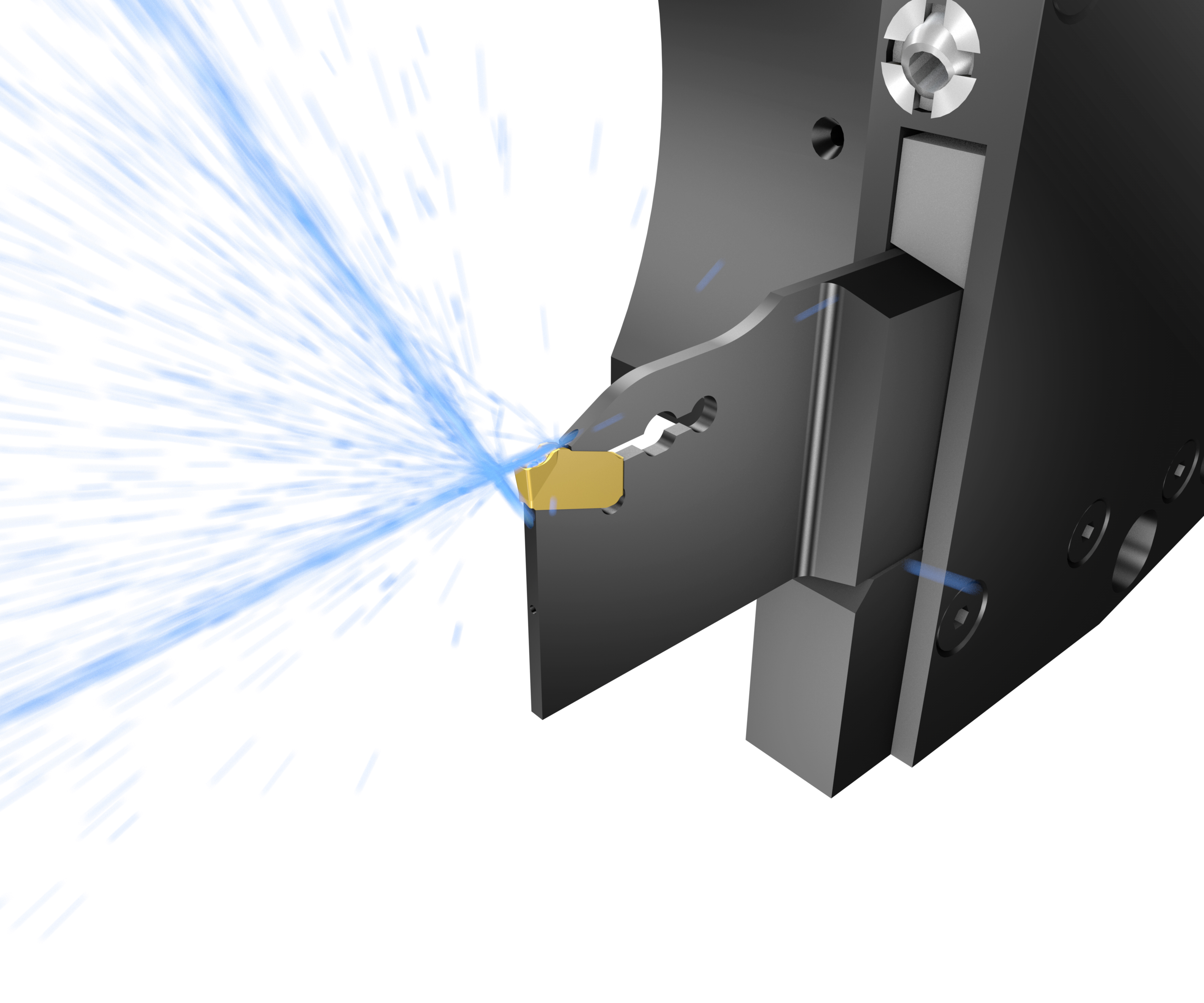
Solve challenges with correctly applied coolant
- Chip control issues: Use over coolant
- Dimensional issues: Normally caused by high temperature – use both over and under coolant and as much pressure as possible
- Short tool life: Use both over and under coolant
- Poor chip evacuation in internal operations: Use both over and under coolant, plus as much high pressure as possible
An important aspect for long tool life and few machine stoppages is good chip control. This is achieved by combining over and under coolant on all tools, which keeps the temperature down at the cutting edge for less tool wear and a more stable performance, while at the same time providing for efficient chip evacuation.
Due to the productivity and performance gains along with the tool life benefits provided with over and under high pressure coolant, Sandvik Coromant has released several new innovative cutting tool solutions to support applications in Turning, Threading, Parting and Grooving, and Milling.
Previously featured on Sandvik Coromant's website.
Brought To You By
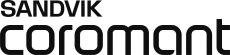
More from Sandvik Coromant
More on How-to
Toolholders are the most important connection between the machine and cutting tool. High-quality toolholders can extend tool life and save you money.
In this episode of MSC Industrial Supply's "How To," host Jacob Sanchez explores the cutting-edge world of tooling and machining innovation with Mitsubishi Materials.
In pipeline construction, properly preparing and cleaning the base material is the first step toward ensuring quality welds and minimizing defects.
Talk to Us!
Interested to evaluate use of high pressure coolant on HMC & VMC which currently has 30bar & 20bar coolant pressure.
The specific operations carried out are drilling, boring, reaming and milling.
Purpose is to avoid continuous chips, improve surface finish, enhance tool life and to reduce intermittent m/c stoppages required to attain any or all of above.
52Leave a reply
Your email address will not be published. Required fields are marked *