Wichita, Kansas, is known as the “Air Capital of the World.” This is due in part to the National Institute for Aviation Research (NIAR) at Wichita State University, a leading advanced aircraft manufacturing laboratory. The area is home to notable aerospace and defense OEMs, including Boeing, the Hawker Beechcraft Corporation, Bombardier Learjet, Cessna, Spirit Aerosystems, and Airbus Americas Inc., to name but a few organizations located here. In the competitive world of advanced aircraft manufacturing, developing world-class talent that can drive innovation is essential to the longevity of the industry. This is where NIAR is uniquely positioned to assist both the local and global need for highly skilled aircraft assembly professionals. Because of the laboratory’s advanced aerospace research, NIAR was selected by President Obama as a manufacturing center.
In the competitive world of advanced aircraft manufacturing, developing world-class talent that can drive innovation is essential to the longevity of the industry.
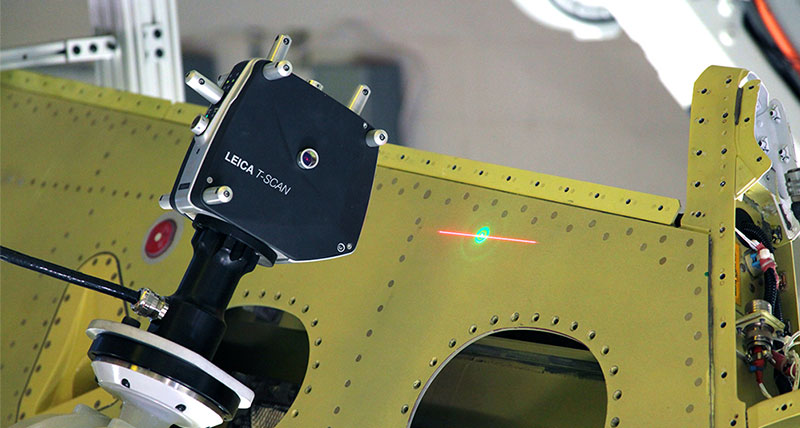
This distinction makes NIAR part of a network of research institutes across the United States focused on developing and commercializing manufacturing technologies through public-private partnerships between U.S. industry, universities, and federal government agencies. The laboratory's value to private industry cannot be understated: as a leading aerospace research organization, NIAR provides test and design services for developing aircraft products. A key initiative for NIAR, and the industry going forward, is determining how to leverage automated manufacturing technologies for improved speed and throughput. Although automobile manufacturers have embraced automation, in part because the production volume is so large, the aerospace industry has been slower to make this investment.
One reason for this is the difference in production volume. Many aircraft manufacturers are considered low volume producers, which has delayed their adoption of automation technologies currently in use on modern automotive OEMs. But that trend is changing, as organizations like NIAR demonstrate that it is easier to employ automation in lower production markets.
Recently, NIAR teamed with Hexagon Manufacturing Intelligence to develop an automated wing surface scanning solution for the aerospace industry. Using a small business jet wing measuring approximately 25' x 6', NIAR and Hexagon engineers were able to reduce a scanning process that previously took all day to less than four minutes. Leveraging the multitasking capabilities afforded by the automated solution, NIAR was able to show on the jet wing that an integrated network of robots, scanning technologies and software tools could accurately and repeatably manage metrology and inspection tasks.
To make this breakthrough, the team used a combination of the Leica Absolute Tracker AT960, and a Leica T Scan 5 mounted to an ABB IRB 4600-40/2.55 robot. Mr. Brian Brown, Director, Robotics and Automation National Institute for Aviation Research, Wichita State University, spearheaded the automation project. Working closely with application engineers from Hexagon Manufacturing Intelligence, they were able to get the automated scanning process up and running in a matter of hours. "Rather than spending hours to days of manual labor inspecting large aerospace components, we can now leverage the Leica T-Scan 5 and ABB Robotics to turn the job into an automated process that only takes minutes," Brown said.
The results were very encouraging. Despite the challenges of scanning a large, metallic finish wing section, the surface scanning data was collected quickly with a high degree of accuracy. NIAR's mission is to be the place "Where Test Plans Become Results" — full structural elements are a focus for this initiative. The ability to rapidly and accurately provide a surface scan of a jet wing is a departure from traditional aircraft metrology processes, offering an automated, accurate and fast way to ensure that aerospace assemblies are fabricated as intended. "Since we can now inspect large aerospace components in minutes rather than hours or days with the use of automation and high end metrology equipment, productivity and efficiency can be greatly increased throughout the entire product line," Brian Brown adds.
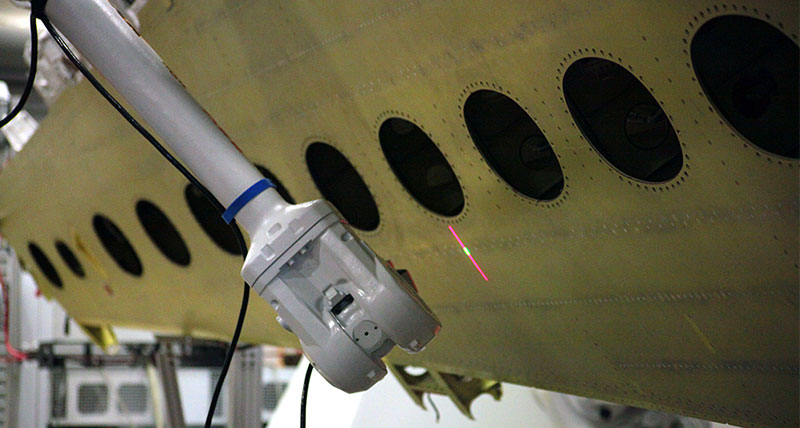
With 20+ laboratories focused on certification testing for airframe technology and a $45 million yearly budget, NIAR is paving the way for advanced aerospace manufacturing processes in the United States. The local economy is powered by aviation manufacturing: Wichita is home to 7,000 engineers and 26,400 aerospace production jobs — 43% of the U.S. generation aviation aircraft is built here.
"As more aviation manufacturing processes become automated, organizations are looking to increase speed, efficiency and precision. By combining the expertise of the labs at Wichita State University and the insights of the Hexagon Manufacturing Intelligence team, high-value, low-cost solutions are developed and implemented quickly and efficiently," Brian Brown concludes.
Previously featured on hexagonmi.com.
Talk to Us!
Leave a reply
Your email address will not be published. Required fields are marked *