As a brand of Saint-Gobain, a world leader in sustainable habitat, Norton offers the widest portfolio of grinding, cutting, blending, finishing and polishing solutions for all markets, materials and applications with the most advanced and affordable technology. So, as your needs evolve, our access to the global expertise of Saint-Gobain becomes even more valuable to making a difference in your day-to-day needs. And, we don’t have to look far for more localized expertise with our largest research center located right nearby in Northboro, MA.
Improving surface finish can be done by making adjustments to one or more of these points: operational parameters, wheel dressing, grit size, coolant delivery and machine condition.
Precision CNC production grinding shines when parts require tight geometric tolerances and quality surface finishes. Typically, surface finishes in the range of 32 microinches Ra to as low as 4.0 microinches Ra and better are the numbers needed to be achieved. Comparatively, a traditional milling or turning operation might achieve a finish of about 125 microinches to 32 microinches Ra.
If the goal is to improve the current surface finish from 20 microinch Ra to 17 microinch Ra, then simply increasing the wheel speed and/or reducing the feed rate slightly might be sufficient. However, if a finer surface finish is required, then these five factors should be addressed.
1) Grinding Operational Parameters
Adjusting the grinding parameters can be the easiest and fastest solution to improve a part’s surface finish. Here are key parameters and recommended actions to do it successfully.
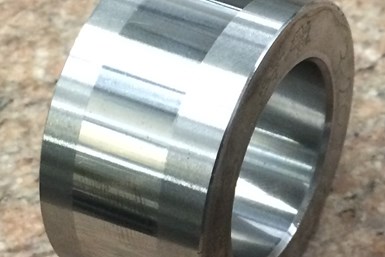
Creep-feed/surface grinding:
- Increase wheel speed. This is a good starting point. However, be sure the wheel is rated to run at the new speed. The maximum operating speed (MOS) will be stated on the side of the wheel.
- Reduce feed rate.
- Reduce depth of cut.
- Increase the number of spark-out passes.
Outer-diameter (OD)/Internal-diameter (ID) grinding:
- Increase wheel speed. As mentioned before, the wheel must be rated to run at the new speed. The maximum operational speed will be stated on the side of the wheel.
- Reduce depth of cut per revolution.
- Reduce work speed (rpm): In-feed rate might need to be adjusted to maintain the depth per revolution.
- Increase dwell/spark-out time.
- Use oscillation (a common practice in plunge ID grinding).
Many grinding machines today have variable speed controllers, so changing the wheel’s speed can be carried out by simply editing the CNC program or adjusting the spindle speed controller. Other machines might require manually changing pulleys and belts.
Reducing the feed rates can also be carried out by editing the CNC program or adjusting the feed rate control. However, this approach can increase the cycle time, which is not always a good option, particularly in a production operation where cycle time is critical. In applications where the cycle time is not critical, reducing the feed rate might be a good option for improving the workpiece surface finish.
When the wheel speed is increased and the depth of cut and feed rate are reduced, the wheel can become dull. This increases the chance of thermal damage to the workpiece and can increase grinding forces. Therefore, care must be taken when adjusting these parameters to not introduce other problems into the process.
2) Grinding Wheel Dressing
The dressing conditions for both conventional and superabrasive grinding wheels can be manipulated to help improve surface finish. This is typically accomplished by slowing down the dress traverse speed and/or reducing the depth-per-pass during dressing. Reducing the dressing depth makes the dressing action less aggressive and results in a smoother wheel face, which typically improves the workpiece surface finish. Reducing the dress traverse speed reduces the dress lead, which is the distance the wheel travels in one rotation of the wheel. The dress lead can be applied to any dressing process where the dressing tool traverses across the wheel face. However, the dress lead does not apply to plunge dressing operations. Adjusting the lead is a good way to improve the surface finish on existing processes.
Talk to Us!
Leave a reply
Your email address will not be published. Required fields are marked *