Q&A with rPlanet Earth: How to Develop a Safety Culture in a Startup
What’s it like for the EHS chief at a startup venture on a mission to achieve zero plastic waste on the planet through a revolutionary approach to producing food-grade packaging from recycled PET? Find out in this interview with Venessa Cardenas, environmental health and safety manager at rPlanet Earth.
When you’re a startup, there’s an opportunity to embrace safety culture from the get-go. We talk to EHS Manager Venessa Cardenas about how that has played out at rPlanet Earth, a unique manufacturer in the plastic recycling and high-recycled content PET packaging industry.
With a mission to help achieve zero plastic waste on the planet, rPlanet Earth has been on a fast and ambitious run for the past couple of years.
The startup built and opened its first plant in Vernon, California, where it recycles plastics to extract polyethylene terephthalate plastic (PET), the chemical name for polyester used in packaging. It then produces food-grade packaging for food, beverage, personal care and other consumer products industries.
“What separates us is we do it all under one roof, which enables us to eliminate several energy-intensive production steps and have the lowest carbon footprint, recycled PET packaging in the world,” says Venessa Cardenas, environmental health and safety manager at rPlanet Earth.
Typically, one company will sort the post-consumer plastic containers that arrive in large bales—“taking out the PET plastic, which is what we’re looking for,” says Cardenas—grind it into flakes and wash them. Next, another company will decontaminate the PET to food-grade quality and either leave it in flake form or melt it into a pellet. Finally, yet another manufacturer will convert the flakes or pellets into food-grade packaging.
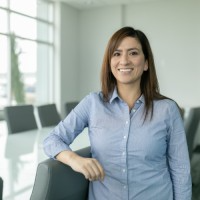
of rPlanet Earth
Despite the frenzy that comes with getting a new venture off the ground, safety has always been a major consideration all along for rPlanet Earth. Cardenas was the ninth employee at the startup.
“It was just management and directors at that point, but they really wanted to bring on an EHS manager early so we weren’t dealing with safety after the fact—after we had employees, after we had an accident,” she says.
Cardenas spoke to Better MRO about the safety focus of her company’s leaders, the building of rPlanet Earth’s EHS practice and how she has tackled the early challenges.
What is it like to be the safety leader at a startup like rPlanet Earth?
Cardenas: It says a lot about the company that they hired me so early on. We were still very much a construction site when I started.
I was one of the earliest starting employees, which really gave me an advantage because I was able to really understand the equipment before we were actually operating it.
Some of it is complex, and there is nothing for reference because we were the first company in the country to have this type of equipment, referring to the Krones Washline and Decontamination lines, the first of their kind in the United States. I had the chance to understand how the equipment works. Overall, it made me a better and more effective environmental health and safety manager.
How did that help with safety culture?
Cardenas: It helped build a great safety culture from the beginning. When the first set of employees were hired on in the summer of 2018, there was already a safety program and a safety culture developed.
I would have to say that one of the biggest things that has been helpful to me is having management support. All the way from our CEOs to the director level—everyone in management really—supports and believes in the importance of the program, which is key to making it successful.
And how do they support the program? Resources—and also just the small things, like following the PPE requirements out on the floor. If our CEOs are out there, they’re wearing steel-toed shoes, hard hats and vests. It shows that no one’s above the rules of the plant.
The other thing that was helpful, being brought on so early, was being able to develop a rapport with the employees, getting to know them, being there from Day 1 when they started.
I’ve always done this in all of my jobs: being out there, walking the floor, talking to the employees, learning why it is that someone is doing something a certain way, asking if there is a better way. When they know you, they’re more open to discussing what they are doing.
We want the employees to know that they can come to us. We’re all learning, and we all want them to feel free to bring up suggestions about how we can do better.
It’s not like it’s a turnkey plant; we’re still learning. It’s a startup. We want the employees to know that they can come to us with any issue and that we take their suggestions seriously. When they see action from their input, that grows the safety culture even further.
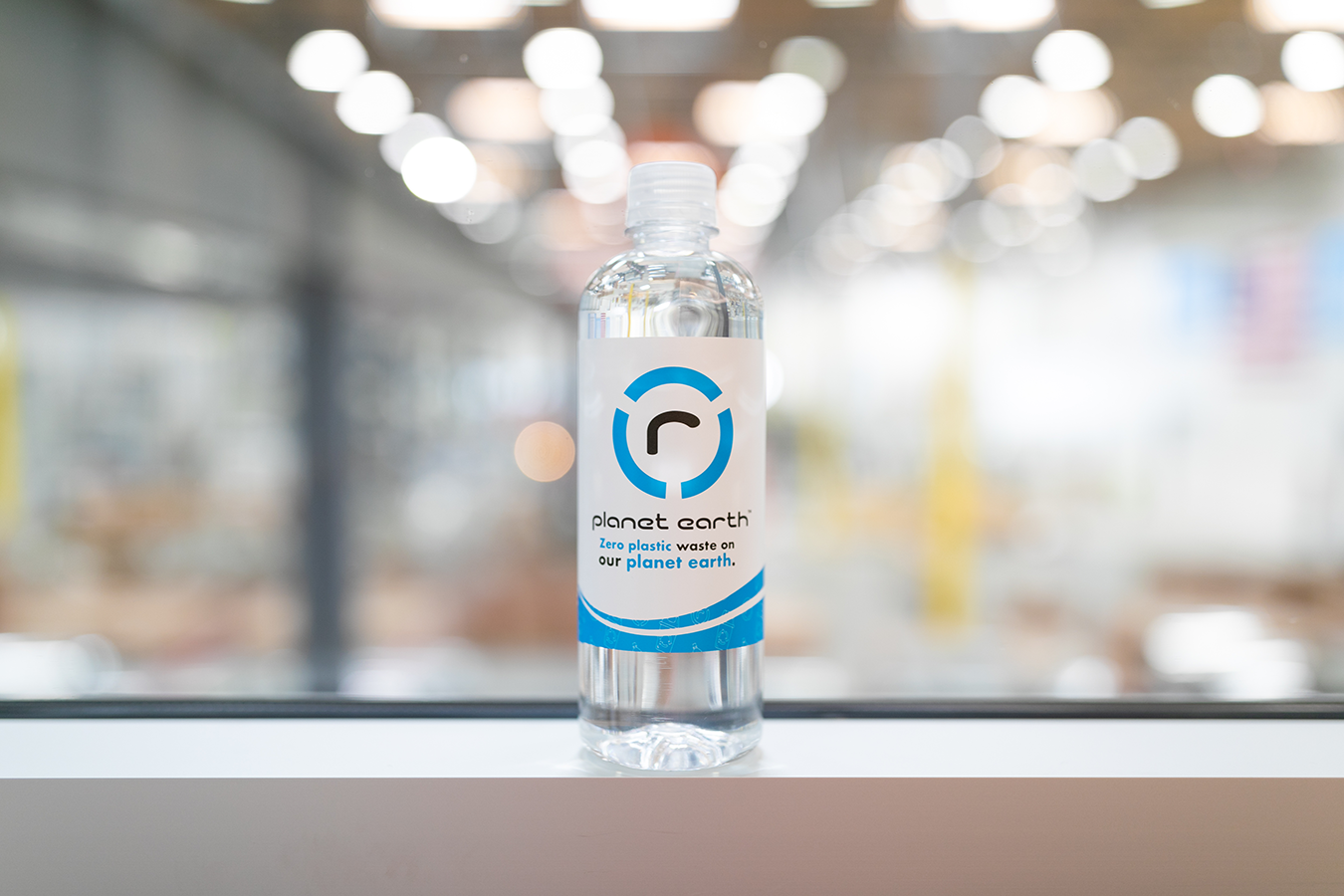
What are some of the safety challenges and hazards in a startup like rPlanet Earth that workers face?
Cardenas: There are definitely potential safety hazards that can come up during the maintenance of the equipment. Because it can sometimes be the first time that a worker or workers must get to a piece of equipment in an area that may have a fall hazard, for example.
For us, first it’s giving them the tools to know, “Hey, that triggers fall protection, and this is a requirement.”
And then, the technicians being comfortable enough to say, “Venessa, this is the first time that we have had to reach this particular part of the machine. From what I remember from our fall protection training, this does trigger fall protection. Can you come and help us figure out what’s the best way to anchor off?”
A lot of times those challenges do come up for us on first-time maintenance—something that we’ve never done before. It’s not like the plant came with a list of all of the things that are potential hazards and everything written out about how we should do things safely.
Instead, it comes up as employees are going through each process and then we work through the safety needs together.
Going back to the management support, there isn’t a rush to just get it done. Instead, they’ve told me to give the employees the authority and encourage them to say, “Hey, this isn’t safe. We need to think this through. I know this needs fall protection. Let’s get the EHS Department so that we know how to tie off properly.”
Fall protection is often surprising for some workers. The height that triggers the need for protection under OSHA standards, 4 feet, doesn’t sound very high at first.
Cardenas: We take it very seriously. We don’t want to put anyone at risk.
We have a good safety record. We had a couple of minor cuts, but nothing else serious. We want to keep it that way.
Your safety team is pretty small, right? How do you keep things covered?
Cardenas: It’s myself, and I have an assistant EHS administrator.
It’s about being creative with your resources.
For example, as we got busy and I was administering forklift training, I leaned on our HR Department, which had a coordinator who had a forklift background. He was able to take over the forklift training class.
You have to be creative about how you can use other resources outside of your department.
You have to be creative about how you can use other resources outside of your department.
How important is ongoing safety training to the culture now that rPlanet Earth is up and running?
Cardenas: It’s very important. How we go about it is as a continuous approach to training.
We don’t let workers go onto the floor on Day 1 until they have gone through their first day of onboarding plant safety and training on all rules applicable to the plant.
Then, every month, we have a different safety topic that we roll through. Recently, it was emergency evacuation and response procedures.
Anyone that’s hired on, once a month we have a full onboarding training of all safety topics. It’s a four-hour session just on EHS-related topics so the new people coming in that month don’t need to wait half a year to get covered on a topic that took place a few months before they joined the company.
I try to make it engaging and interesting by giving out candy and prizes since there is a lot of information to go through.
The other thing that we do are inspections and audits of the floor. We use these as a training tool. We generate a report; it gets sent to all the managers; we discuss it.
Managers know that it’s very important to share the information with their teams, so they use each report as their own training update tool. At their daily and weekly shift meetings, they’re sharing the findings with the employees. They’re reminding everyone of the things that they need to be aware of.
How do you manage the tools and PPE that your workers need to be safe? You mentioned anchors, for instance, but given rPlanet Earth’s work, your PPE use is extensive.
Cardenas: One of the best things that we recently implemented is the MSC inventory management vending solution. All of our general use PPE—gloves, glasses, Tyvek suits, face shields—are stocked in this machine now.
Initially, we managed all of that manually. We’re trying to get to the place where it’s all process-oriented. Someone comes from MSC once a week and makes sure we have the minimum stock of supplies. If not, then they order it and stock it.
As to fall protection, we have issued harnesses to the people who have gone through training. Everyone who has been trained gets their own individual harness.
We have a spreadsheet that details each harness’s identification number, when the harness was issued and who it was assigned to. That way when we do our quarterly inspections, we have that list to reference. It’s not very technical, but it works for fall protection.
All other PPE is managed via the MSC vending machine.
What about some of the fall protection gear that’s not assigned specifically to an individual?
Cardenas: Although fall protection is manually managed and we just rolled out the vending machine, I’m working with MSC to see if there is a way to use the machine to check out some of the fall protection equipment, like beam anchors and self-retracting lifelines.
What’s great about the machine is that you can limit who can access things and check them out. That ensures it’s only the people who need a specific item and have gone through appropriate training can check an item out—and put it back.
.png)
I would expect lockout/tagout has been a heavy focus for you?
Cardenas: When I joined the company, that was one of the first things I started to work on—even when some of the equipment was still in crates on the factory floor.
It goes back to being willing to be fluid and knowing which equipment was going to run first and that it was going to need a lockout/tagout procedure. Lockout/tagout were the first procedures that we drafted.
We’re still refining lockout/tagout procedures as we go because some of the equipment is very complicated. The procedures have to be based on how workers interact with the equipment, which is learned over time.
On our wash line, for example, there are certain stages when the workers have to clean the equipment. The lockout/tagout for that is basically a work instruction—step by step: “If you’re going to clean this machine, this is where you put your lock,” and then going through the steps of how to clean.
There continues to be a big focus right now on drafting work instructions and incorporating the safety procedures. Each policy emphasizes if you’re doing a certain task, this is the PPE required, this is the tool that you need, and, if there’s lockout/tagout, these are the lockout/tagout points that you need to follow.
Does having multiple people involved in safety—from EHS and senior management to HR and the people out on the floor—help bolster rPlanet Earth’s safety culture by making everyone responsible for safety?
Cardenas: Exactly. I’m a department of two, and this is a 300,000-square-foot plant that is working toward becoming a 24/7/365 operation. I’m out there; I make my rounds; I show a presence and see what’s going on.
But there also is a big expectation for the managers to take responsibility for their departments because I’m not going to be able to see everything. I’m not always out there. We do drive responsibility to the managers and supervisors of the departments.
It’s about being resourceful because you cannot do everything yourself. That comes down to if there is a near-miss, knowing that the managers complete the report forms.
Right now, we’re in the process of training them how to do their own EHS inspections. I was doing them all by myself, but now we’re starting to involve representatives from other departments so that they can walk along and learn what we’re looking for, and they can start generating the inspection reports, too.
When it comes to getting buy-in from senior management, what are the things that are important to be able to share?
Cardenas: Our senior managers are really big on employee retainment. It’s what drives them. Happy employees are going to stick around. There are direct and indirect costs if you have lots of employee turnover.
That goes down to giving great health benefits, providing healthy foods to employees every day at no cost and providing steel-toed shoes to the employees. We provide a $125 voucher every year for new shoes as well as a prescription safety glasses benefit.
It hasn’t been difficult to sell things like that to our CEOs because they are very much on board with keeping the employees happy. They know if our employees are happy, that retention levels will be high and they’ll take good care of rPlanet Earth.
Talk about that impact on the employees.
Cardenas: We really do want to invest in our employees. At the end of the day, we don’t want to just keep them in the same positions. If someone is willing to learn, we want to progress them in their career.
From a safety perspective, they see that and they appreciate that. In the end, if you take care of the employees, they will take care of you.
There are so many positive impacts that come along with a great safety culture: employee retention, fewer workers’ comp injuries and better-quality workmanship, just to name a few. People care, and they take pride in their work. In the end, that helps the company.
If you have happy employees, your company is going to work so much more smoothly. I think some companies forget that because of the costs incurred for investing in safety. But there are so many indirect savings that go along with keeping your employees safe.
It all just comes down to taking care of the employees.
Has your safety experience been similar? Share what you have learned.
Talk to Us!
Leave a reply
Your email address will not be published. Required fields are marked *