In business for over 80 years AccuformNMC is the leading manufacturer of American made safety communication products—including over 16,000 safety signs, tags, and labels. Our commitment is to support every safety ID need, with the best product, service and custom solutions in the industry. We offer the toughest signs and labels in the market, and guarantee them for life. Protected with Sign Muscle®, a clear liquid over-laminate strong enough to protect against fading under direct sunlight, it allows easy graffiti removal, resists chemical corrosion and is applied for free.
Electrical shocks can occur wherever electricity is in use and employers must take measures to protect their workers.
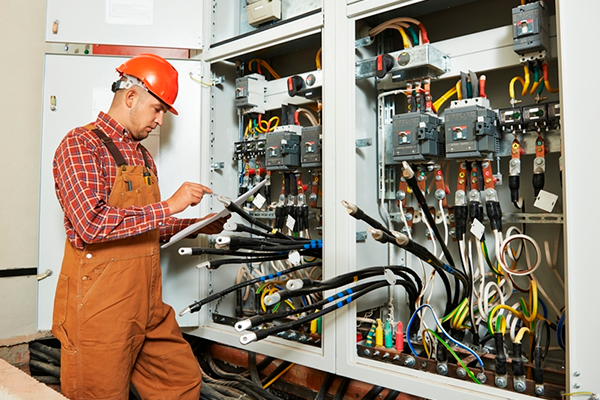
The Occupational Health and Safety Administration recognizes four common workplace safety hazards that can easily become fatal if the right precautions aren’t in place ahead of time. In the first entry of this four-part series, we’ll examine electrical hazards – one of OSHA’s “Fatal Four” and a hazard that can strike anytime, often without warning.
Dangers of electrical shock
In this day and age, electricity is everywhere – it’s all but impossible to find a workplace that doesn’t use it, in some form or another. That’s what makes it such an important hazard to guard against: It affects workplaces ranging from industrial manufacturers to financial offices.
While the incidence of electrical shock is relatively low, the damage can be exceedingly high, according to the National Fire Protection Association. Those incidents that do occur are more likely to cause severe injury or death than many more common workplace accidents. Data from the U.S. Bureau of Labor Statistics showed that 961 injuries occurred from electrical exposure from 2008 to 2010. Of those 961, 525 resulted proved fatal – a rate of 55 percent.
While the construction industry accounts for roughly half of the electrical shock fatalities reported between 2004 and 2013, the remainder are divided fairly evenly between Professional and Business Services, Trade, Transportation and Utilities, Natural Resources and Mining, and Manufacturing. Additionally, the number of worker fatalities attributed to electrical shock has been steadily declining as more employers address hazards proactively.
How employers can prevent electrical shock
There are two sides to shock prevention: mitigating the ability of a piece of equipment to cause injury and educating employees on safe practices.
In many cases, faulty equipment can cause shocks unexpectedly. Arc flash can occur during a short circuit and shock an individual who isn’t even physically touching an electrical cabinet, for example. Unexpected equipment start-up can also cause electrical shock. In both of these cases, a lockout tag can help individuals recognize when a piece of equipment is or is not safe for use. Employers should make an effort to install safety guards on equipment that could energize and shock workers.
Educating workers on best safety practices is also essential. Individuals who presume a certain level of safety, fail to adhere to protocol, or forget to don necessary safety equipment can put themselves and others at risk of electrical shock or fire, according to OSHA. Safety signs play a major role in reminding employees to take the correct steps, avoid certain areas and perform other important safety-related tasks.
Electrical shocks can occur wherever electricity is in use and employers must take measures to protect their workers.
Previously featured on National Marker Company.
Brought To You By
.png?itok=k2IwFSM2)
More from AccuformNMC
More on Employee Safety
Using the right lockout/tagout gear is vital to protecting some 3 million employees from machinery hazards. Discover four ways to optimize your lockout/tagout system to prevent incidents and stay compliant with OSHA safety standards.
Even the most safety-conscious employers might lose sight of a hidden hazard: puncture wounds. Mechanix Wear experts discuss glove technology that combines safety, comfort and productivity.
Millions of workers are exposed to metalworking fluids every day. Manufacturing businesses need to understand the risks that metalworking fluids pose to people, the regulations to comply with, and the steps to take to protect employees.
Talk to Us!
As a 30 year veteran of industrial electrical maintenance my main concern while troubleshooting live electrical equipment has been the actions of bystanders. Too often it is the overly curious non-trades personnel who compromise the safety of the technician performing an inherently dangerous task. Often, management folks are failing to advise those folks to be mindful and respectful of this. As skilled-trades positions are becoming harder to fill, too few managers are asking those already performing this work, why has this situation developed in the U.S.A.
41Very good point, Allen. Thank you for your feedback.
27That was a really useful post, at the same time would you consider checking out -
<a href="https://molec.com.au">Molec</a> our company with 30 years of expertise
which provides hazardous area and commercial electrical services at a best price. call us at 03 9315 1200.
35Leave a reply
Your email address will not be published. Required fields are marked *