The aim of ergonomics in manufacturing is to design workstations that encourage healthy work postures and maintain worker comfort and safety. Here are steps employers can take to minimize ergonomic hazards in their facilities.
Bending, twisting, turning and lifting heavy objects—these are common body movements for manufacturing workers, and they can result in painful injuries for a worker and, sometimes, costly periods of time away from work for recovery.
An injury related to this kind of work is called a musculoskeletal disorder (or MSD), sometimes also referred to as an “ergonomic injury.” It occurs when your body “uses muscles, tendons and ligaments to perform tasks, usually in awkward positions or in frequent activities which, over time, can create pain and injury,” according to the U.S. Bureau of Labor Statistics (BLS).
MSDs account for nearly 70 million physician office visits in the United States each year and around 130 million healthcare encounters, including outpatient, hospital and emergency room visits, according to research from the National Research Council and the Institute of Medicine.
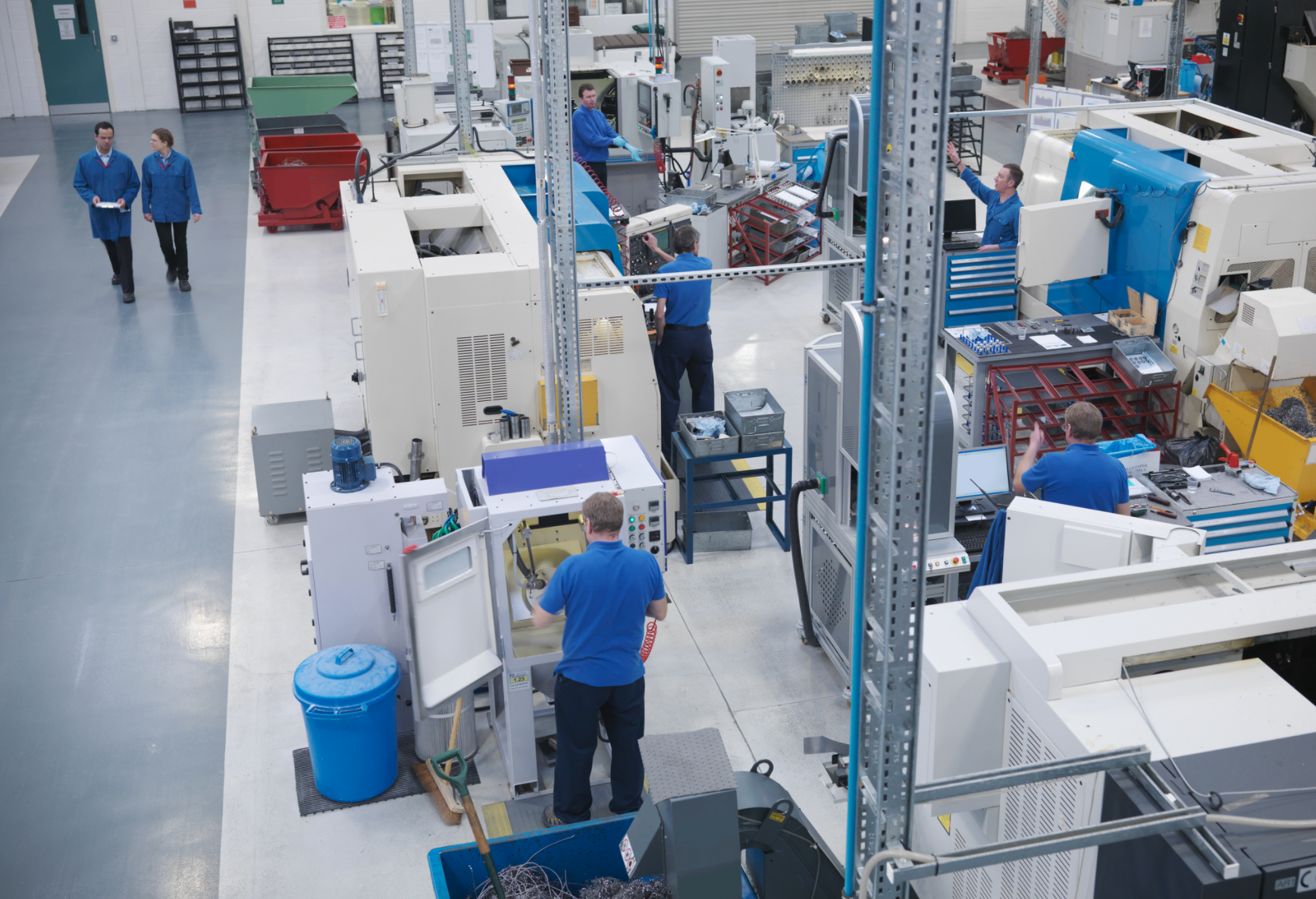
Examples of the kinds of injuries caused include carpal or tarsal tunnel syndrome and other connective tissue disorders that result from overexertion or bodily reaction, according to the BLS. Overexertion and repetitive motion are the primary causes of these injuries.
Disabling workplace injuries cost U.S. businesses more than $59 billion annually, as they lead to time away from work, extended periods of recovery and workers’ compensation claims.
An effective ergonomics program reduces the risk of injury to your workers while maintaining or improving their health, leading to happier, healthier workers and fewer workdays lost to injuries and compensation claims. The idea is to design the job to fit the worker, not physically forcing the worker’s body to fit the job.
Solutions may include improving workstation design to minimize potential injuries, using flooring to minimize fatigue, or investing in help from robots and other technological innovations. Here are three solutions and best practices that can help improve ergonomics in your facility.
No. 1: Designing Ergonomic Workstations
Industrial ergonomic workstations are created to accommodate workers and adapt to their physical attributes rather than forcing a worker to adapt to his or her work environment.
Using a poorly designed workstation or completing a task using an improper method can put a worker at risk of injury. By designing and arranging work environments in a way that provides employees with a relaxed working position, where tasks follow the body’s natural movements, potential injuries may be reduced, prevented or eliminated.
For example, dynamic shelving, storage and picking solutions bring items from a storage area to your production, assembly or packing station, ensuring needed parts are at hand and workers do not have to fetch and carry items.
“Making these changes has reduced physical demands, eliminated unnecessary movements, lowered injury rates and their associated workers’ compensation costs, and reduced employee turnover. In many cases, work efficiency and productivity have increased as well.”
Other solutions may include organizer bins that minimize clutter around workstations and floor mats that reduce worker fatigue after long periods of standing, which both help to improve safety by reducing the possibility of injuries.
The most effective ergonomics programs consider the risks faced by each worker at his or her workstation. In the past, this has been achieved by hiring ergonomics experts to assess workplaces and train employees. But many companies do not have the budget required for this kind of training. Thankfully, simple, low-cost solutions are often available to solve problems.
As the Occupational Safety and Health Administration notes, many industries have successfully implemented ergonomic solutions in their facilities to minimize MSD injury risks.
These interventions have included “modifying existing equipment, making changes in work practices and purchasing new tools or other devices to assist in the production process,” OSHA says. “Making these changes has reduced physical demands, eliminated unnecessary movements, lowered injury rates and their associated workers’ compensation costs, and reduced employee turnover. In many cases, work efficiency and productivity have increased as well.”
Read more: Manufacturing Efficiency: 5 Ways to Maximize Shop Floor Space
No. 2: Harnessing Helpful Technology
Technological advances are helping companies to manage the problem of worker injuries.
According to EHS Today, over the last few years big manufacturers such as Toyota, Ford and Boeing have started to use devices called exoskeletons, which are hard mechanical frames with joints that allow a human operator wearing one to move.
Similar to the exoskeletons seen in nature, typically on insects or crustaceans, a robotic exoskeleton is worn externally by a human and is protective. It also augments and supports humans when they are performing a variety of tasks, reducing the likelihood of muscle strain or injury.
As EHS Today notes, overexertion “continues to be a leading cause of pain, physical disability, missed work, lost productivity, turnover and medical expenses,” with the Centers for Disease Control and Prevention (CDC) identifying back pain as the most prevalent work-related health problem.
Employers pay more than $1 billion per week for direct workers’ compensation costs for disabling, nonfatal workplace injuries, which explains why technologies such as exoskeletons “are becoming a popular investment to ensure worker safety, well-being and productivity,” EHS Today notes.
As the technology has become more practical and affordable, smaller companies in industries such as construction, agriculture and manufacturing have started using exoskeletons. The CDC has issued a report outlining the potential risks and benefits of this technology.
Other technologies helping to alleviate injuries at work include collaborative robots, or cobots, which are tabletop robots that can be programmed to handle repetitive, dirty or dangerous tasks, letting companies move existing employees into more satisfying roles. Cobots are designed to work alongside humans in the workplace. They are smaller, lighter and more affordable than traditional robots, boosting competitiveness and flexibility in almost any company.
Read more: How Using Automation in Facilities Helps to Reduce Workplace Injuries
No. 3: Mental Health: Handling Cognitive Overload
While traditional manufacturing and industrial ergonomics has focused on reducing a worker’s physical fatigue and discomfort to lessen safety hazards, more modern assessments are looking at “cognitive ergonomics,” which essentially means considering the cognitive load placed on workers.
According to a report in ISE Magazine, the member magazine of the Institute of Industrial and Systems Engineers, cognitive ergonomics examines how work affects people relative to their “attention distribution, decision-making, cognitive aspects of mental load, stress and human errors.”
The idea is that a significant “cognitive load” can have a detrimental impact on a worker’s performance by slowing performance and increasing errors. As employees do more work with technology and other sophisticated tools related to manufacturing’s Industry 4.0—such as the Industrial Internet of Things (IIoT) —and less work that requires physical strength, there is a greater need for problem-solving and reasoning skills.
Solutions to this problem may include digital training applications that help streamline the learning procedure for new technologies, real-time analytics dashboards to simplify how data are gathered and interpreted, investing in human error reduction training programs, or simply giving workers enough time away from tasks to replenish their mental energies.
What steps are you taking to reduce injuries that occur as a result of poor ergonomics or cognitive overload? Share your thoughts in the comments below
Talk to Us!
do you have stock name to invest into your company
59Thanks for the interest, here is the info:
NYSE: MSM
90Like to Try a skeleton
how can i get it and the cost ?
107Setiw excelente y de mucha ayuda
57Leave a reply
Your email address will not be published. Required fields are marked *