Tooling Up is a video series by MSC Industrial Supply Company that provides real-world insights brought to you by leading industry experts and aimed at improving the efficiency and productivity of your operations. Through Tooling Up, you’ll gain access to our knowledgeable in-house specialists and experts from our most-trusted partners and suppliers, along with some exclusive innovative offerings from MSC. From metalworking and MRO supplies, services, and expertise, to inventory management solutions, and to the safety and well-being of your team, we are dedicated to working side-by-side with you to make your operations better.
Video Highlights
In this episode of MSC's Tooling Up, Toni Neary sits down with Mike Browner, Product Manager for Sensors and Scales at Mitutoyo, to explore the latest advancements in surface measurement technology. Mike discusses the details of Mitutoyo's non-contact inline sensors, emphasizing their precision, ease of integration, and game-changing impact on factory automation. The conversation highlights the remarkable 20-micron accuracy of the current model and teases the upcoming release of a 9 micron sensor, marking a new frontier in measurement solutions. Mike also discusses how real-time data collection is helping manufacturers reduce scrap and improve production efficiency. Join Toni and Mike as they uncover how Mitutoyo continues to set the standard for precision and innovation in the industry.
To find out more about Mitutoyo's surface scanners, visit MSCDirect.com.
For even more metalworking insights and expertise check out MSC's Better MRO knowledge hub.
For more Tooling Up videos, check out our MSC Tooling Up playlist.
For a full transcript of the video, click here
In this episode of MSC's Tooling Up, host Toni Neary is joined by Mike Browner, Product Manager for Sensors and Scales at Mitutoyo, to explore the fascinating world of surface measurement technology.
Video Transcript
MIKE BROWNER: This sensor works using a diffused light laser. So it bounces light off of the product and then uses that either build a 2D profile or a 3D surface view of an object, and these have a guaranteed accuracy of 20 microns, like I said.
Narrator: This video is brought to you by Mitutoyo. Precision is our profession. If you're looking for real world insights, tips from leading industry experts, the latest trends in products and technology, you've come to the right place. From MSC Industrial Supply, this is Tooling Up.
TONI NEARY: Hello and welcome to Tooling Up. I'm your host, Toni Neary, and I'm so glad that you've joined us here today. Before we get started, go ahead and click those like and subscribe buttons so you never miss a single episode of Tooling Up. All right, everybody subscribed? Great. Let's dive in today. I'm excited. We're going to be talking about surface measurement sensors.
And we have Mike Browner, the product manager for sensors and scales at Mitutoyo. Mike, thanks for joining us. And welcome to Tooling Up.
MIKE BROWNER: Hi. Thank you for having me.
TONI NEARY: So before we get into surface measurement, let's dig beneath the surface. Sorry. Pun intended. Tell us a little bit about how you ended up at Mitutoyo.
MIKE BROWNER: Well, I've been in linear motion in mechatronics and factory automation for about 18 years now. I've started here about a year ago. I was, I actually switched over to flame and vapor control and got bored because I couldn't blow anything up. And I noticed a position at Mitutoyo. And I've used their tools my whole career, and I thought it was a great opportunity to come see what I could do with my skills here.
TONI NEARY: I love that, and I love the fact that you can blow things up. So you found a job that was a little bit more stable. So when we talk about specializing in factory automation and using Mitutoyo, obviously one of the top brands in the industry, tell me a little bit about what makes Mitutoyo so special for you.
MIKE BROWNER: We have a great motto, good people, good technique, good products. And I've always found that to be really interesting. We're truly dedicated to making the most precise products we can. We want our products to be quality and want our products to be reliable. So we've always spent that extra time making sure that we provide the best measurement solutions and always improve our performance and accuracies.
TONI NEARY: And I didn't know that there was a more precise, more precise than precise precision. But would you say the new surface measure sensor is ultra-precise?
MIKE BROWNER: Absolutely. The accuracy on the model I just released is 20 microns. It's the best I found in its class. I'm in the process of actually releasing a 9 micron accuracy model, which would be the second model in the line.
TONI NEARY: So tell me a little bit about the non-contact inline sensor, because I think it's different in how the technology actually approaches surface measurement.
MIKE BROWNER: Absolutely. This sensor works using a diffused light laser. So it bounces light off of the product and then uses that to either build a 2D profile or a 3D surface view of an object. And these have a guaranteed accuracy of 20 microns, like I said.
TONI NEARY: So when you talk about the in-line sensor, you're not talking about roller blades, right? Why is inline so important?
MIKE BROWNER: Absolutely. Inline is important because it really helps to improve efficiency. While it's in-line it's being inspected as it's moving. It gives people the ability to make corrections on the fly versus now, which is done more offline or near lines. So people are taking parts off the assembly line and inspecting them while they're inspecting and things are still being made.
So really there could be something wrong that they're just finding out. And while they're finding it out, bad parts are being made. That ends up leading to a lot of scrap and a lot of inefficiencies.
TONI NEARY: Well, and I know we talked about it, one of the problems with that is you could get an entire pallet that you're ending up scrapping, whereas when you're actually using the sensor and it's just part of your production line, it's running a little bit more smoothly, right?
MIKE BROWNER: Absolutely. That some production lines are extremely high speed. They can make up to a whole pallet of parts while they're inspecting. They find a few bad ones and they have to make the decision whether they want to inspect that whole pallet or scrap it. And most of the time it ends up leading to scrapping it because it's just more cost-effective that way.
TONI NEARY: So Mike, I think one of the top topics that we're hearing right now in the industry is all about automation. And I don't think people are considering automation when it comes to inspection and looking at parts as they're moving through a production line. So can you tell me, is there an easy way to implement automation in a production line for companies and organizations out there that are looking to streamline the process?
MIKE BROWNER: You can really design a machine to do any job you want, or look for space in an existing cell to integrate sensors. Some people have staffs to do that on but at the other time, a lot of people are going to integrators. They're fantastic groups of people. They can design a machine, implement a sensor, commission it, and get everything running for you so that you're able to get running as quickly as possible.
TONI NEARY: And I think one of the coolest things about this technology is really the data, because it's not just about inspecting the component that's coming through. But tell me a little bit about the data you're collecting and how shops can actually use that to become more efficient.
MIKE BROWNER: Oh, absolutely. So if you collect all your data using an SPC system, you're able to look at how many defects you have, when the defects are, what kind of defects you have, and all kinds of various aspects of the manufacturing system, and start making high level decisions as to what kind of changes you need to make or what kind of adjustments you need to make.
TONI NEARY: And I think it's really important that we're looking at, you know, reducing scrap. And what are your customers telling you about implementing these sensors and reducing scraps? Do you have any, you know, anecdotal stories or any great feedback from customers so far?
MIKE BROWNER: Yeah, actually I've got a couple of the people I'm working with in automotive industry. They're making high volume parts. It gets back to that. Pallets of parts being scrapped. They again same thing. They, they pull parts offline, they start making inspections. Their machines are moving so fast that they're pretty much if they don't catch an error right away, they are throwing away a pallet full of 10,000 parts versus getting the sensor installed, learning how to program it, figuring out where the data goes. And then again, once they have that data, they can start looking at improving their process in other ways.
TONI NEARY: And I think it's amazing when we look at Mitutoyo and we look at innovation, really the two go hand in hand. You're looking at top-of-the-line precision, top-of-the-line innovation. I have to ask, will there be more coming out in this new sensor line?
MIKE BROWNER: Absolutely. In the, just started the process of releasing the next model, which is actually an even higher accuracy of 9 microns, a little bit shorter of a measuring range, though, and hopefully by the end of this year I will be releasing our next, the third model, which will actually have a little bit longer of a measuring range, but it will be 50 microns.
Again, though, as I took a look at some of the competitors’ models, we really look like we're still going to be the most accurate in class for both of those. So at Mitutoyo, accuracy is our business.
TONI NEARY: So Mike, the sensors are one component here. But I think we also have to talk about the software because I think that's where it can tend to get a little tricky. Do you need to buy software to go along with these sensors?
MIKE BROWNER: No you don't. Actually, with our models, the software is included with the sensor. There's no licensing fees, there's no fee to update. There's no additional cost whatsoever for any of the software. If we make any updates to it in the future, those will absolutely be free too. Everything is included and you're ready to go once you get the unit.
TONI NEARY: Fantastic. Mike, I cannot thank you enough for your time today and your passion and really just being innovative in the market.
MIKE BROWNER: Thank you.
TONI NEARY: It was great hanging out with Mike today, and if you enjoyed the conversation as much as I did, make sure that you go ahead and like and subscribe to our channel so you don't miss any upcoming episodes. To find out more about surface measure sensors, visit https://www.mscdirect.com/products/mitutoyo-laserscanner. Thanks so much and we'll see you next time on Tooling Up.
Narrator: Want more insights and ideas to improve the efficiency and productivity of your operations? Check out the Tooling Up Video playlist to hear tips that can take your company to the next level, and subscribe to our channel so you won't miss out.
Brought To You By
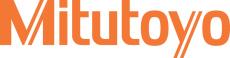
Headquartered in Aurora, IL, Mitutoyo America Corporation is the world's largest provider of measurement and inspection solutions offering the most complete selection of machines, sensors, systems and services with a line encompassing CMM (coordinate measuring machines), vision, form and finish measuring machines, as well as precision tools and instruments, and metrology data management software. Mitutoyo's nationwide network of Metrology Centers and support operations provides application, calibration, service, repair and educational programs to ensure that our 8,500+ metrology products will deliver measurement solutions for our customers throughout their lifetime.
Related Articles
The TESA TLC-BLE wireless Bluetooth® emitter allows you to connect measuring instruments to a computer.
Say goodbye to sluggish readings with the QuantuMike from Mitutoyo. Its patented ratchet mechanism ensures a constant measuring force, eliminating guesswork.
The new Starrett W4900 Electronic Indicator combines innovation, high versatility and ease-of-use with unparalleled ease of settings navigation.
Talk to Us!
Leave a reply
Your email address will not be published. Required fields are marked *